Follow along with the video below to see how to install our site as a web app on your home screen.
Note: This feature may not be available in some browsers.


Largest Manufacturing Technology Community on the Web

- Search Forum Discussions
- Search Entire Site
- Advanced Search
- Employer Products
- Employer Dashboard
- Job Seeker Dashboard
- REGISTER FREE

- Search forums
- Specific Machine Forums
217 thermal trip alarm
- Thread starter dmitch9072
- Start date Apr 29, 2010
- Views 38,265
- Apr 29, 2010
We have a Mazak VTC20B with an M32B control. I am getting a 217 thermal trip alarm. Can anyone tell me what that is pointing to?
Check your alarm lists, but it sounds like your invertor unit is getting hot. Try blowing the dust out, see if this helps.
I think it is the coolant pump heating up. The machine runs fine until you turn the pump on for a minute or so then it kicks out. Thanks,
- Sep 10, 2012
dmitch9072 said: I think it is the coolant pump heating up. Click to expand...
- Sep 11, 2012
Check your chip conveyor is it jammed?
- Sep 13, 2012
Check your coolant pump the inlet screen on the underside is packed with chips, this causes mine to trip.

- Sep 14, 2012
Clean out the chips and other garbage that collects inside the fan shroud, do the HYD pump while your at it.
wippin' boy
thermal trip is mazak speak for a tripped motor overload it means a motor is jamed or burned up the "thermal" part is refering to a thermal overload seeing a higher than normal current draw which is sensed by the temp in overload portion of the motor starter
- Jun 20, 2014
Greetings. I am having the same problem with the same machine and although I tried everything that was suggested nothing happens. We replaced the (cooling) oil in the pump, we disassembled the pump and we changed the mechanical bearing. Nothing! Oil system works fine, but the pump is getting hot. I do not have the manual but the switch that trips is QF12. From a Russian manual I found that QF12 refers to the ventilation (fan) of the radiator. We measured it. Electric-wise everything is fine, but we changed it as well. Nothing. Any idea as to what could be the remedy? Thanks a lot in advance
- Jul 29, 2014
I managed to solve the problem and I want to inform you, as I might give a clue to someone facing similar situation(s). I made a mistake on translating two words from a russian manual I found. The problem was on the ventilation unit of the spindle (fan). We replaced it and it works fine now. Thanks again

RossEngTech
- Aug 9, 2017
Another possibility Just to add to this thread for future issues. I had the 217 alarm as well but none of the above turned out to be the issue. What it did end up being faulty was a sticky contactor. So developing a troubleshooting plan should include identifying what is wrong first (the 217 alarm is a general overload alarm, from Mazak themselves) and then checking the possibilities in the system starting with the easiest and most likely to the more complicated and harder to check. I had almost given up and requested a tech in when I decided to give it one more go around and included the contactors in the check. Lesson learned, do not discount anything.
- Oct 6, 2023
We have the same alarm (general thermal alarm) on our Mazak HCN 4000. It is tripping QF56 and displays "fan" in the list but QF56 is not in the wiring diagram book. I think it is spindle cooling fan.
- Mar 12, 2024
If you have a mist collector, you may try looking at that.
Similar threads
- Mar 13, 2024
- Jan 14, 2024
- CNC Machining
- Feb 16, 2024
- DriversEd72
- Mar 26, 2024
- Sep 25, 2023

This website or its third-party tools process personal data (e.g. browsing data or IP addresses) and use cookies or other identifiers, which are necessary for its functioning and required to achieve the purposes illustrated in the cookie policy. To learn more, please refer to the cookie policy . In case of sale of your personal information, you may opt out by sending us an email via our Contact Us page. To find out more about the categories of personal information collected and the purposes for which such information will be used, please refer to our privacy policy . You accept the use of cookies or other identifiers by closing or dismissing this notice, by scrolling this page, by clicking a link or button or by continuing to browse otherwise.
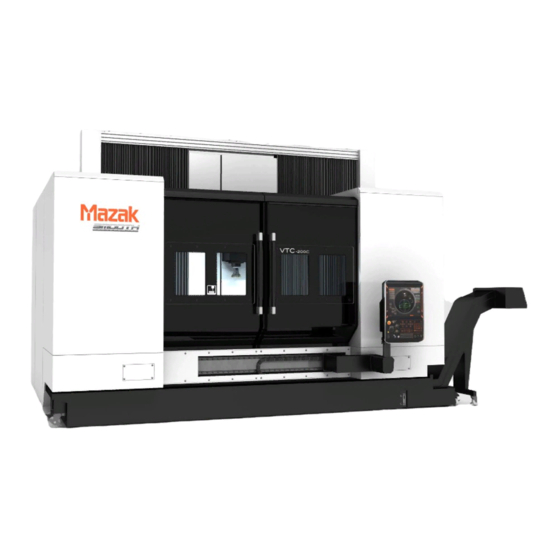
- Mazak Manuals
- Industrial Equipment
- Operating manual
Mazak VTC-200B Operating Manual
- Maintenance manual (97 pages)
- page of 530 Go / 530
Table of Contents
1 introduction.
- List of Related Manuals and Documents
- Numbering of Figures and Tables
2 Safety Precautions
- Basic Safety Items
- Clothing and Personal Safety
- Operational Safety
- Safety Considerations Relating to Holding Workpieces and Tooling
- Maintenance Safety
- Workplace Safety
- Safety Considerations Relating to Chip Conveyor
- Safety Equipment
- 2-10 Remarks on the Cutting Conditions Recommended by the NC
- 2-11 Safety Nameplates
1 Outline of the Machine
- Axis Definitions
- Names and Locations of Machine Units
2 Operation Panels
- Locations of Operation Panels
- Arrangement of Switches on the NC Operation Panel
- Names and Functions of Switches and Other Controls on the NC Operation Panel
- Auxiliary Operation Panel
- Data Input/Output Panel
- Magazine Operation Panel
- Main Power Disconnect Switch
- MACHINE SET up Switch (Key-Lock Type Switch)
3 Manual Operation
- Inspection before Starting Operation
- Switching the Power on
- Inspection after Switching the Power on
- Switching the Power off
- Zero-Point Return
- Warmup Operation
- Starting the Spindle
- Stopping the Spindle
- Jogging the Spindle
- Changing the Direction of Spindle Rotation
- Rapid Traverse Operation
- Cutting Feed Operation
- Pulse Handle Feed Operation
- Clearing the Soft-Limit Alarm
- Coolant System Operation
- 3-10-1 Manual ATC Operation
- 3-10-2 Recovering ATC Operation after Interruption
- Chip Conveyor Operation (Optional Specifications)
4 Preparing for Machining
- Procedure for Mounting Tools to the Magazine
- Procedure for Removing Tools from the Magazine
- Restrictions on Tools
- Dimensional Restrictions on Workpieces
- Procedure for Mounting and Removing Workpieces
- Measuring Coordinate Values
- Selection of Coolant
- Replenishing Coolant
- Major Machine Specifications
- Stroke Diagram and Spindle Interference Diagrams
- Spindle Speed-Power-Torque Diagrams
- Sub Table Dimensions
- Workpiece Interference Diagram
Advertisement
Quick Links
- 1 Table of Contents
- 2 List of Related Manuals and Documents
- 3 Alarm List
- 4 Code List
- Download this manual
- Section 1 27
- Section 2 41
Related Manuals for Mazak VTC-200B
Summary of contents for mazak vtc-200b.
- Page 1 This Manual is published to assist experienced personnel on the operation, maintenance and/or programming of Mazak machine tools. All Mazak machine tools are engineered with a number of safety devices to protect personnel and equipment from injury or damage. Operators should not, however, rely...
- Page 2 Return to Library Notes:...
- Page 3 Return to Library VTC-200B,200C & 300C Operation............ SAFETY PRECAUTIONS ..............LOCKOUT PROCEDURE ................. INSTALLATION PRECAUTIONS ..............WARNINGS ....................... Sec. 1: Introduction ................1 INTRODUCTION .................... 1-1 List of Related Manuals and Documents ............... 1-2 Pagination ........................1-3 Numbering of Figures and Tables .................
- Page 4 Return to Library 2-2-2 Names and Functions of Switches and Other Controls on the NC Operation ..2-3 Auxiliary Operation Panel ....................2-4 Data Input/Output Panel ....................2-10 2-5 Magazine Operation Panel .................... 2-11 2-6 Main Power Disconnect Switch ..................2-12 2-7 Operators Door Interlock ....................
- Page 5 Return to Library Sec. 3: Operating NC Unit & Preparation for Auto Operation ..CONTENTS ....................... 1 PREPARATION FOR AUTOMATIC OPERATION ......... 1-1 Preparation Steps for Automatic Operation ..............2 DISPLAY OVERVIEW ..................2-1 Name of the Components of Each Display ..............
- Page 6 Return to Library 5-1 TOOL LAYOUT Display ....................5-1-1 Data display ......................5-1-2 Tool layout procedure ..................5-1-3 Clearing pocket numbers ..................5-1-4 Specifying a spare tool ..................5-1-5 Erasing spare tool data ..................5-1-6 Erasing procedures for registered tool data ............
- Page 7 Return to Library 6-4 PLANE CHECK Window ....................6-22 6-4-1 Data display ......................6-22 6-1-2 Displaying machining shape ................6-23 6-1-3 Others ........................6-23 6-5 SECTION CHECK Window ................... 6-23 6-5-1 Data display ......................6-24 6-1-2 Displaying sectional shapes ................6-25 6-1-3 Others ........................
- Page 8 Return to Library 7-1-1 Data display ......................7-23 7-1-2 Registering milling tool data ................7-25 7-1-3 Erasing a part of the registered data ..............7-29 7-3 TOOL OFFSET Display ....................7-30 7-3-1 Data display ......................7-30 7-1-2 Tool-compensation data setting procedures ............
- Page 9 Return to Library 10-1-2 Display modes ....................10-15 10-7 DIAGNOSIS (MAKER) VERSION Display ..............10-18 10-1-1 Data display ....................... 10-18 10-8 DIAGNOSIS (MAKER) DIAGNOSIS MONITOR Display .......... 10-19 10-1-1 Data display ....................... 10-19 10-1-2 Display operations ..................... 10-20 10-9 DIAGNOSIS (MAKER) OPTION Display ..............
- Page 10 Return to Library 11-7 EIA/ISO Conversion ....................11-98 11-7-1 Outline ....................... 11-98 11-7-2 EIA conversion program format ................. 11-99 11-7-3 Output data unit ....................11-99 11-1-4 Operating procedure ..................11-100 11-1-5 Supplementary description and precautions for conversion of ......11-100 11-1-6 Parameter and alarm lists ..................
- Page 11 Return to Library 2-11-2 Function description ..................2-10 3 CHANGING THE CUTTING CONDITIONS ........... 3-1 Rapid Feed Override ..................... 3-1-1 Procedure ......................3-2 Cutting Feed Override ....................3-2-1 Procedure ......................3-3 Spindle Speed Override ....................3-3-1 Procedure ......................3-4 VFC Function ........................
- Page 12 Return to Library 1-1 Major Machine Specifications - VTC-200B ..............1-2 Stroke Diagram and Spindle Interference Diagrams - VTC-200B ......... 1-3 Spindle Speed-Power-Torque Diagrams ............... 1-4 Table Dimensions ......................1-5 Sub table Dimensions ....................1-6 Workpiece Interference Diagram ................... 2 ALARM LIST - VTC-200/300 (MAZATROL FUSION 640M) ......
- Page 13 Return to Library SAFETY PRECAUTIONS 6) Do not deface, scratch or remove any caution The machine is provided with a number of safety plate. Should it become illegible or missing, devices to protect personnel and equipment from order another caution plate from the supplier, injury and damage.
- Page 14 Return to Library • AFTER CONTROL POWER IS TURNED ON CAUTION: When the control power “ON” switch on the 4) Tools and other items around the machine or operating panel is on, the "READY" lamp on equipment should be stored to ensure good the operating panel should also be on (check to footing and clear aisles.
- Page 15 Return to Library CAUTION: CAUTION: 1) Thoroughly read and understand the safety precautions in the instruction manual. 1) During automatic operation, never open the 2) Thoroughly read whole maintenance machine door. Machines equipped with the manual and fully understand the principles, door interlock will set the program to single construction and precautions involved.
- Page 16 Return to Library WARNING ALWAYS TURN THE MAIN CIRCUIT BREAKER TO THE “OFF” POSITION & USE AN APPROVED LOCKOUT DEVICE WHEN COMPLETING MAINTENANCE OR REPAIRS. THE LOCKOUT PROCEDURE THAT FOLLOWS IS INTENDED TO SAFEGUARD PERSONNEL & EQUIPMENT DURING MAINTENANCE OPERATIONS, AND, REPRESENTS THE MINIMUM REQUIREMENTS.
- Page 17 Ambient temperature during machine accuracy alignment operation: 0° thru 45°C (32°F to 113°F). specifications quoted by Mazak can usually 2) Avoid areas where the humidity fluctuates be obtained when the minimum foundation greatly and/or if high humidity is present; requirements are met.
- Page 18 Return to Library • WIRING 1) Use only electrical conductors with performance ratings equivalent or superior. 2) Do not connect any power cables for devices Desirable Independent Grounding: which can cause line noise to the power distribution panel, such as arc welders and high frequency machinery.
- Page 19 In such cases, the machine tool end user is required to supply the necessary circuit breaker or switching device. FAILURE TO COMPLY CAN RESULT IN PERSONAL INJURY AND DAMAGE TO THE MACHINE. IF ANY QUESTION EXISTS, CONTACT THE NEAREST MAZAK SERVICE CENTER FOR ASSISTANCE.
- Page 20 TOOL TO IDENTIFY THE REQUIRED PARAMETERS TO CHANGE. FAILURE TO COMPLY WITH THESE INSTRUCTIONS COULD RESULT IN DAMAGE TO THE MACHINE, SERIOUS INJURY OR DEATH. IF ANY QUESTIONS EXIST, CONTACT THE NEAREST MAZAK SERVICE CENTER FOR ASSISTANCE. WARNING MAZAK MACHINES ARE ENGINEERED WITH A NUMBER OF SAFETY DEVICES TO PROTECT PERSONNEL AND EQUIPMENT FROM INJURY AND DAMAGE.
- Page 21 MAINTENANCE AND DETAIL SPECIFICATION DOCUMENTATION SUPPLIED WITH THE MACHINE AND BY THE TOOLING MANUFACTURER. NOTE: THE MAXIMUM INSERT WEIGHT FOR MAZAK MACHINES IS 20 gf. (0.04 lbs.). FAILURE TO COMPLY WITH THESE INSTRUCTIONS COULD RESULT IN DAMAGE TO THE MACHINE, SERIOUS INJURY OR DEATH.
- Page 22 TO WITHSTAND CUTTING FORCES DURING WORKPIECE MACHINING. FAILURE TO COMPLY WITH THESE INSTRUCTIONS COULD RESULT IN DAMAGE TO THE MACHINE, SERIOUS INJURY OR DEATH. IF ANY QUESTIONS EXIST, CONTACT THE NEAREST MAZAK SERVICE CENTER FOR ASSISTANCE. WARNING CONFIRM PROPER WORKPIECE FIXTURING/CLAMPING, TOOL SETUP AND THAT THE MACHINE DOOR IS SECURELY CLOSED BEFORE THE START OF MACHINING.
- Page 23 How easy are the manuals to understand? Are the illustrations helpful? Overall, how do you rate the documentation? What did you like about the documentation? How can it be improved? RETURN TO: MAZAK Corporation Technical Publication Dept. 8025 Production Drive Florence, Kentucky 41042...
- Page 24 Return to Library Notes:...
- Page 25 Return to Library...
- Page 26 Return to Library Notes:...
Page 27: Table Of Contents
- Page 28 Return to Library - MEMO -...
Page 29: Introduction
Page 30: numbering of figures and tables, page 31: safety precautions.
- Page 32 Mazak and mount the replacement in the original position. (If a nameplate has been lost, obtain the part number from the “Parts List”...
Page 33: Clothing And Personal Safety
Page 34: safety considerations relating to holding workpieces and tooling, page 35: maintenance safety, page 36: workplace safety, page 37: safety equipment, page 38: 2-10 remarks on the cutting conditions recommended by the nc.
- Page 39 Return to Library...
- Page 40 Return to Library Notes:...
- Page 41 Return to Library TABLE OF CONTENTS (MACHINE OPERATION) Page OUTLINE OF THE MACHINE ..............1-1 Axis Definitions ....................1-1 Names and Locations of Machine Units............. 1-2 OPERATION PANELS................2-1 Locations of Operation Panels ................2-1 NC Operation Panel ................... 2-2 2-2-1 Arrangement of Switches on the NC Operation Panel ........... 2-3 2-2-2 Names and Functions of Switches and Other Controls on the NC Operation Panel........................
- Page 42 Return to Library Switching the Power OFF .................. 3-6 Zero-Point Return....................3-7 Warmup Operation..................... 3-9 Spindle Operation .................... 3-10 3-7-1 Starting the Spindle ..................... 3-10 3-7-2 Stopping the Spindle ................... 3-10 3-7-3 Jogging the Spindle..................... 3-10 3-7-4 Changing the Direction of Spindle Rotation ............3-11 Feed Operation ....................
- Page 43 Return to Library 4-1-3 Restrictions on Tools..................... 4-5 Mounting and Removing Workpieces..............4-6 4-2-1 Dimensional Restrictions on Workpieces............... 4-6 4-2-2 Procedure for Mounting and Removing Workpieces..........4-7 4-2-3 Measuring Coordinate Values ................4-7 Preparing Coolant ....................4-8 4-3-1 Selection of Coolant ....................4-8 4-3-2 Replenishing Coolant ....................
- Page 44 Return to Library - MEMO -...
Page 45: Outline Of The Machine
Page 46: names and locations of machine units, page 47: operation panels, page 48: nc operation panel, page 49: arrangement of switches on the nc operation panel, page 50: names and functions of switches and other controls on the nc operation panel.
- Page 51 Return to Library Table 2-1 Names and Functions of the Switches on the NC Operation Panel The numbers in the table below correspond to the numbers given in Figs. 2-3 and 2-4. Name Function • Power ON button Used to switch on the power to the NC unit. When this button is pressed, the “READY”...
- Page 52 Return to Library Name Function RESET key • Used to reset the NC to the initial state. If an alarm is displayed, eliminate the cause of the alarm and press this key to clear the alarm display. • Spindle speed override keys Use to adjust the spindle speed.
- Page 53 Return to Library Name Function MDI key • Used to select the MDI mode. Press this key to automatically execute the manually set data. MEMORY key • Used to select the memory operation mode. Press this key to execute a program stored in the NC memory. TAPE key •...
- Page 54 Return to Library Name Function Machine READY indicator • Comes on when the CNC gets ready for controlling the machine. Status lamp Indicator HDD WARM UP • Comes on when the hard disk is warmed by the heater. Lamps indicator lamp If ambient temperature is low and the hard disk cannot start correctly, it is warmed by the heater.
Page 55: Auxiliary Operation Panel
Page 56: data input/output panel, page 57: magazine operation panel, page 58: main power disconnect switch, page 59: operator's door interlock.
- Page 60 Return to Library Actions to be taken after an occurrence of door interlock function related alarm To continue the operation after the occurrence of an alarm caused by opening the operator’s door, close the door and clear the alarm message. The procedure to be followed to continue the interrupted operation is indicated below.
Page 61: Manual Operation
- Page 62 Return to Library Magazine Operator’s door Hydraulic pressure gauge Hydraulic until level gauge Control panel door Coolant tank oil level gauge Centralized lubrication unit oil level gauge Spindle cooling fluid Air pressure gauge level gauge Fig. 3-1 Inspection before Starting Operation...
Page 63: Switching The Power On
- Page 64 Return to Library If an abnormality is found when the hydraulic unit starts, press the (POWER OFF) button or the emergency stop button. The hydraulic unit stops operating. If the “EMERGENCY STOP” message is displayed in red at the lower left area of the POSITION screen when the power is switched on, it indicates that one of the emergency stop buttons is locked in the activated position.
Page 65: Inspection After Switching The Power On
Page 66: switching the power off, page 67: zero-point return.
- Page 68 Return to Library Remark 1: If an axis is moved beyond the travel range by mistake, the soft-limit function operates to stop the axis. If this occurs, the soft-limit alarm indication is displayed at the lower left area in the screen. The procedure to be followed for clearing the soft-limit alarm is explained in section 3-8-4 “Clearing the Soft-Limit Alarm”.
Page 69: Warmup Operation
Page 70: spindle operation, page 71: changing the direction of spindle rotation, page 72: pulse handle feed operation, page 73: clearing the soft-limit alarm.
- Page 74 Return to Library Cleaning the soft-limit alarm If an axis fails to move continuously due to the occurrence of a soft-limit alarm, move the axis in the opposite direction. Example: Soft-limit alarm has occurred during axis feed of the X-axis in the positive direction by using the pulse handle.
Page 75: Coolant System Operation
Page 76: 3-10 atc operation.
- Page 77 Return to Library ATC operation Turning the ATC arm to 52゚ ゚ ゚ ゚ The ATC arm cannot be turned to 52゚ unless the following conditions are satisfied: • X- and Y-axis are at the second zero point. • Spindle is oriented. •...
- Page 78 Return to Library Others Perform the ATC cover open operation. Follow the same steps as (1) and (2) in item 3. A. Press the [ATC COVR OPEN] menu key. Perform the ATC cover close operation. Follow the same steps as (1) and (2) in item 3. A. Press the [ATC COVR CLOSE] menu key.
- Page 79 Return to Library Unclamp the spindle tool. <If spindle orientation has not been completed> (1) Follow the same steps as (1) and (2) in item 3. A. (2) Press the [UNCLAMP OK] menu key. (3) Place the TOOL UNCLAMP switch in the position.
Page 80: 3-10-2 Recovering Atc Operation After Interruption
- Page 81 Return to Library Manually turn the ATC arm to any position. Recovering an interrupted ATC operation by pressing the reset switch If the reset switch has been pressed when the Y-axis and Z-axis were at the second zero- point respectively: Follow the same steps as explained in item 1.
Page 82: Chip Conveyor Operation (Optional Specifications)
- Page 83 Return to Library Operation procedure l In daily operation, the chip conveyor must be kept operating in the forward direction disregarding of whether or not chips are being generated. l If large volume of chips are put into the chip conveyor at a time, chips will be stuck in the CAUTION conveyor, causing the conveyor to stop.
- Page 84 Return to Library - MEMO - 3-24...
Page 85: Preparing For Machining
- Page 86 Return to Library Align the tool pocket key with the keyway in the tool and insert the tool into the tool pocket. Confirm that the tool has been mounted completely in the tool pocket. Close the magazine door. If the magazine door is left open, the magazine will not rotate in any operation mode, manual or automatic.
- Page 87 Return to Library Precautions on Mounting the Tools When mounting a tool such as a back boring bar or fine boring bar which must be shifted at the bottom of finished hole so that the cutting tip will leave a scratch in tool retraction motion, care must be paid in the direction of the cutting bit.
Page 88: Procedure For Removing Tools From The Magazine
Page 89: restrictions on tools, page 90: mounting and removing workpieces, page 91: procedure for mounting and removing workpieces, page 92: preparing coolant, page 93: adjustment of coolant nozzle direction.
- Page 94 Return to Library - MEMO - 4-10...
- Page 95 Return to Library Return to Library...
- Page 96 Return to Library...
- Page 97 Return to Library MAZATROL FUSION 640M NC OPERATION SAFETY PRECAUTIONS ..............Lockout Procedure .................... Installation Precautions ..................Warnings ......................1 PREPARATION FOR AUTOMATIC OPERATION ......1-1 Preparation Steps for Automatic Operation ..........2 DISPLAY OVERVIEW ..............2-1 Name of the Components of Each Display ..........
- Page 98 Return to Library 4-1-4 Change of scale values ....................4-3 EIA MONITOR Display ................4-11 4-1-1 Data display ....................... 4-11 4-1-2 EIA/ISO monitor function .................... 4-12 4-1-3 Editing functions ......................4-12 4-1-4 Restart 2 unmodal function ..................4-13 4-4 MACHINING - MONITORING Display ............
- Page 99 Return to Library 5-5 Manual Measurement ................. 5-22 5-5-1 Function overview ...................... 5-22 5-5-2 Use of manual measurement ..................5-22 5-1-3 Measurement pattern ....................5-23 5-1-4 MEASURE display ..................... 5-27 5-1-5 Mode changeover ...................... 5-29 5-1-6 Measuring procedure ....................5-30 5-1-7 Other functions ......................
- Page 100 Return to Library 6-1-2 Displaying machining shape ..................6-23 6-1-3 Others ........................6-23 6-5 SECTION CHECK Window ................. 6-23 6-5-1 Data display ....................... 6-24 6-1-2 Displaying sectional shapes ..................6-25 6-1-3 Others ........................6-25 6-6 PROGRAM FILE Display ................6-26 6-6-1 Data display .......................
- Page 101 Return to Library 6-9-1 Data display ....................... 6-40 6-1-2 Displaying data ......................6-43 6-1-3 Display modes ......................6-44 6-1-4 Modifying the cutting conditions ................. 6-46 7 DISPLAYS RELATED TO TOOLS ........... 7-1 TOOL DATA Display ................... 7-1-1 Data display ....................... 7-1-2 Tool-data input procedures (for MAZATROL programs) ..........
- Page 102 Return to Library 8-2-2 Data registration ......................8-3 USER PARAMETER Display ..............8-3-1 Data display ....................... 8-4 MACHINE PARAMETER Display ............... 8-10 8-4-1 Data display ....................... 8-10 9 DISPLAY RELATED TO DATA STORAGE ........9-1 DATA I/O Display ..................9-1-1 Data display .......................
- Page 103 Return to Library 10-6-1 Data display ......................10-12 10-1-2 Display modes ......................10-15 10-7 DIAGNOSIS (MAKER) VERSION Display ..........10-18 10-1-1 Data display ......................10-18 10-8 DIAGNOSIS (MAKER) DIAGNOSIS MONITOR Display ......10-19 10-1-1 Data display ......................10-19 10-1-2 Display operations ....................
- Page 104 Return to Library 11-4-2 Detailed description ....................11-76 11-1-3 Hold Status ....................... 11-81 11-1-4 Notes ........................11-82 11-1-5 Parameters ....................... 11-82 11-1-6 Appendix ........................11-83 11-5 Hard Disk Operating Function ..............11-86 11-5-1 Outline ........................11-86 11-5-2 Preparation for HD operation ...................
- Page 105 Return to Library PREPARATION FOR AUTOMATIC OPERATION To machine workpieces, you must mount the tools for machining to the magazine and prepare jigs. For automatic operation, programs and other various data must be set to the NC. This chapter describes procedures to be carried out before automatic operation. Preparation Steps for Automatic Operation Supposing that the tooling and adjustment of each part for operation have already been completed, the subsequent operational steps are described below.
- Page 106 Return to Library Preparation of part drawings Reflection of mounting workpiece TOOL FILE display PROGRAM display Preparation of machining Recording of tools program available in the workshop SHAPE CHECK display Verification of the programmed shape TOOL DATA display TOOL LAYOUT display Verification of the tools Registering of tools to be mounted on the magazine...
- Page 107 Return to Library DISPLAY OVERVIEW Name of the Components of Each Display The liquid crystal display unit of the operation panel presents a specific display according to the particular requirements. All displays are composed of the display areas shown below. D735S1001 Name Name...
- Page 108 Return to Library Message display area Directions for operation and data descriptions are displayed in inquiry form. “ ” The character strings displayed here are referred to as messages Data input area Data that has been set using address/numeric data keys is displayed. Data display area Data that has been input, data that the NC unit has processed, and other informations specific to the current display are displayed.
- Page 109 These displays are used to register the control elements (parameters) of the NC unit or machine and the data for automatic decision of cutting conditions. Data that YAMAZAKI MAZAK recommends is displayed; you can add or change data as required.
- Page 110 Return to Library Configuration of Displays Configuration of displays MONITOR PART SHAPE WORK No. POSITION HANDLE COMPARISON RESTART INTERRUPT STOP∗ PALLET MACRO WORK OFFSET TRACE MEASURE ∗ MANAGEMENT MONITOR VARIABLE ∗ ∗ WORK No. WORK No. POSITION PROGRAM MONITOR POSITION PART SHAPE MONITOR RESTART...
- Page 111 Return to Library DATA I/O WORK No. ADDITIONAL SPINDLE LOAD MACHINING MACHINING- GRAPHIC NAVIGATION- MONITORING ∗ DISPLAY RESULT POSITION TOOL LAYOUT WORK No. CUTTING CONDITION CUTTING CONDITION LEARN Main display Sub-display MAINTENANCE GRAPHIC Window CHECK MAINTENANCE ∗ Optional The displays connected by the line can be called up mutually by pressing menu key.
- Page 112 Return to Library 2-3-1 DISPLAY MAP display Function: The names of the displays that the NC unit can create are listed here. Remarks: - This display gives a grouped list of display names which can be displayed on the following eight displays: •POSITION display •PROGRAM display...
- Page 113 Return to Library Display data description Item Unit Data description Names of the displays that can be directly selected from the POSITION display. POSITION • • Names of the displays that can be directly selected from the PROGRAM display. PROGRAM •...
- Page 114 Return to Library Erasing windows Basically, windows that have been displayed by the selection from the menu bar or by pressing the corresponding menu key can be erased by repeating the same selection from the menu bar or by pressing that menu key once again, respectively. Note: Several certain windows will be auto-erased if a menu key or the display selector key is pressed or if numeric data is set.
- Page 115 Return to Library Displays on which the Window name Description of window display window can be displayed POSITION Same as the current position displayed on the POSITION display - MACRO VARIABLE - TOOL OFFSET - WORK OFFSET - ADDITIONAL WPC PROGRAM Display of the MAZATROL program of the unit where the cursor remains - PROGRAM LAYOUT...
- Page 116 Return to Library - NOTE - 2-10...
- Page 117 Return to Library DATA SETTING METHODS Registration of data in the NC unit is accomplished by setting data in each item displayed on the LCD unit. This chapter describes general methods of setting, erasing and modifying data, and related precautions. More specific methods of setting data are described in each section for operating display.
- Page 118 Return to Library Setting Data and Address Set data and address using this procedure: Place the cursor on the intended item. - Press one of the cursor keys and move the cursor to the intended item. - If the cursor does not appear on the CRT screen, press one of the cursor keys and then when the cursor is displayed, move it to the intended item.
- Page 119 Return to Library Selecting Menu Data Use this procedure to set non-numeric/alphabetic data: Place the cursor on the intended item. - See the description of step (1) in Section 3-1 above. Select data item from the menu displayed. Î Selected data item is displayed at the position where the cursor has been placed. Note 1: In the remainder of this manual, selecting data from a menu will be called “menu data selection”.
- Page 120 Return to Library Modifying Data Modify data as follows: Place the cursor in the position where the data to be modified is displayed. - See the description of step (1) in Section 3-1. Set new data. Î The data at the cursor position is overridden with the new data. Incremental Input During data setting, you may see the function name INCRMENT INPUT in a menu.
- Page 121 Return to Library DISPLAYS RELATED TO THE MACHINE OPERATIONAL STATUS POSITION Display Function: This display shows various types of information about the operational status of the machine and the workpiece-machining status. Remarks: When the POSITION display is selected, the various functions required for manual operation or automatic operation will be displayed at the menu display area.
- Page 122 Return to Library Displayed data when the COMMAND menu item is reversed D735S1006E Display data description Item Unit Data description Current position of the tool tip on each axis in the workpiece coordinate X,Y,Z (inch) system Current • position mm (inch) Current position of the tool tip on each axis in the workpiece coordinate 4,5,6 or degrees...
- Page 123 Return to Library Item Unit Data description Actual quantity of machined workpieces, and the preset number of workpieces to be machined (Parts count) ( b ) Pieces • a• Actual quantity of machined workpieces b• Preset number of workpieces to be machined - The number and name of the tool currently mounted in the spindle - If an eight-digit T-command code is set, the number of the tool being used will be displayed at TNo.
- Page 124 Return to Library Item Unit Data description Degrees or Current position of the tool tip in the workpiece coordinate system (only 4,5,6 mm (inch) when an additional axis is provided) Current position of the machine in the machine coordinate system X,Y,Z (inch) •...
- Page 125 Return to Library 4-1-2 Data registration On the POSITION display, the following data can be registered: Parts count Number of machined workpieces (a, item •) After machining, the total number of machined workpieces will be calculated and displayed at a of item •, if “1”...
- Page 126 Return to Library 4-1-3 Display operations Work number selection Any of the work numbers displayed on the POSITION display (that is, the work numbers of the programs which can be used for automatic operation) can be selected. The procedure is as follows: Press the WORK No.
- Page 127 Return to Library 4-2-1 Data display Displayed data D735S1007E Display data description Item Unit Data description Machining shape that has been defined by the program (Shape) (For point-machining, this data is displayed with a purple line. For line- or • face-machining, this data is displayed with a green line.) •...
- Page 128 Return to Library 4-1-2 Displaying machining shape and tool tip Press the WORK No. menu key Î The display status of WORK No. will then be reversed. Press the numeric key(s) that corresponds to the work number of the program to be executed, and then press the INPUT key.
- Page 129 Return to Library 4-1-3 Plane select Press the PLANE CHANGE menu key. Î The following menu will then be displayed in the menu display area: XY-XZ YX-YZ • 3-D display Single-plane Dual-plane Press the menu key that corresponds to the plane or 3-D view to be selected. Î...
- Page 130 Return to Library Press the PART SHAPE menu key. - The available machining shapes will be displayed continuously at the new scaling factor. If 3-D view has been selected If the 3-D menu key has been pressed during plane-select operation, the 3-D display viewpoint can be changed.
- Page 131 Return to Library EIA MONITOR Display Function: - The currently active block is displayed in a reverse-display status on the program list. - During block stop, the program section that succeeds the block just completed can be edited. - The program can be restarted by specifying its starting position using the cursor on the program list.
- Page 132 Return to Library 4-1-2 EIA/ISO monitor function The EIA/ISO program that has been selected on the POSITION display are listed on this display. During automatic operation, the currently active block is displayed in a reverse-display status (the program scrolls as operation progresses, and the active section is continually displayed on the screen).
- Page 133 Return to Library Note 2: An alarm will result if the CYCLE START button is pressed during program editing on this display. Before pressing the CYCLE START button, be sure to terminate the program editing operation by pressing the ROGRAM COMPLETE menu key. 4-1-4 Restart 2 unmodal function Move the cursor to the block line to be selected.
- Page 134 Return to Library MACHINING - MONITORING Display Function: - Displaying the changes in the machining load of the spindle and each axis, in the spindle speed, and the output characteristics of the spindle. - Setting the threshold for the cutting-load detection type of drill auto-pecking cycle. 4-4-1 Data display Displayed data with normal display of DRILL MONITOR menu item...
- Page 135 Return to Library Displayed data with reverse display of DRILL MONITOR menu item  '  *  +  ,  -  (  )  $  0  .  / D735S1102E Display data description Item Unit Data description - Work number of the program being executed...
- Page 136 Return to Library Item Unit Data description - Graphic display of spindle output characteristics or changes in machining load of the spindle and feed axes. ( a ) a: Graph number b: Graph title 1. For a graph of spindle output characteristics c: Spindle output (kW) –1 d: Spindle speed (min...
- Page 137 Return to Library Item Unit Data description - Graphic display of the machining torque of the spindle. Graphic display • • a: Machining torque (N•m) b: Sampling time (sec) c: Machining torque of the spindle is displayed in a green line. Red and yellow lines refer respectively to the peak value (for the displayed data samplings) and the threshold for pecking by a drill.
- Page 138 Return to Library 4-1-3 Selecting graphs to be displayed in the machining-monitoring mode Two or four graphs can be displayed at the same time in the machining-monitoring mode. - Four-graph display mode Four graphs are displayed squarely at the same time. Process monitoring data from the past of a maximum of 80 seconds to the present is displayed in this mode.
- Page 139 Return to Library Press the 2 GRAPH (or 4 GRAPH) menu key. Î The display of the menu item will be reversed and the following dialogue box for graph selection will appear: (A) 2-graph display mode (B) 4-graph display mode Using the Tab key and the cursor keys, select the type of graph for each display section.
- Page 140 Return to Library Note 1: Even if the threshold is changed during execution of the cutting-load detection-type drill auto-pecking cycle, that new value will not become valid until the machining cycle is completed. Note 2: Do not perform the cutting-load detection type of drill auto-pecking cycle if the drill has a tool diameter of 4 mm or less or is made of a material other than high-speed steel.
- Page 141 Return to Library Using the cursor keys, select a time scale as required. - The knob displayed in the dialogue box can be moved by pressing a cursor key. Moving the knob to the right (LONG) or the left (SHORT) prolongs or shortens the time which corresponds to the right end of the abscissa for the graphs concerned.
- Page 142 Return to Library - NOTE - 4-22...
- Page 143 Return to Library DISPLAYS RELATED TO MACHINING SET UP TOOL LAYOUT Display Function: - This display is used on the screen when assigning pocket numbers to the tools to be used for machining or erasing the registered tool names. Remarks: - The operation of assigning pocket numbers to the tools to be used is referred to as tool layout.
- Page 144 Return to Library Display data description ITEM UNIT Data description Pocket number for the current tools CURRENT PKNO. • • Tool name for the current tools CURRENT TOOL • • mm (inch) Nominal diameter of the current tools CURRENT ACT-φ •...
- Page 145 Return to Library Pocket-number shift If there are the same tools as those which are already registered on the CURRENT display among the tools being indicated on the NEXT display, it is no longer necessary then to assign pocket numbers to such tools. That is, the pocket numbers that have already been assigned can be shifted as they are.
- Page 146 Return to Library those with pocket numbers of 0 (undetermined) are automatically assigned serial pocket numbers, starting with the top tool name on the display first. Note: In this method, the data being indicated on the CURRENT display will be disregarded.
- Page 147 Return to Library Manual pocket-number and tool interference data assignment This method is one in which the tools being indicated on the NEXT display are respectively assigned serial pocket numbers and tool interference data one by one. (C-1) Press the cursor key to call the cursor on the screen. (C-2) Press the the cursor key to move the cursor to the row of the tool name to which a pocket number must be assigned is displayed.
- Page 148 Return to Library (C-5) Press the menu key that corresponds to the tool interference data you want to set. Î The tool interference data will be displayed at the cursor. - In the example shown above, press the LARGE L menu key. The display will then change as follows: WNo.123 NEXT...
- Page 149 Return to Library WNo.123 CURRENT NEXT PKNo. TOOL ACT-φ STATUS PKNo. TOOL ACT-φ PKNo. TOOL ACT-φ DRILL That is, the tool names with pocket numbers assigned on the NEXT display will be indicated in order of pocket number on the CURRENT display. The chamfering cutter with a nominal diameter of 20 mm that has been registered under pocket number 4 will be erased automatically (see Note above).
- Page 150 Return to Library 5-1-4 Specifying a spare tool If the tool data being indicated on the NEXT display includes the data of the tool which needs a spare tool, it is possible to specify the spare tool on this display. Press the cursor key to call the cursor on the NEXT display.
- Page 151 Return to Library 5-1-5 Erasing spare tool data Proceed as follows to erase specified spare tool data: Press the cursor key to move the cursor to the PKNo. item of the spare tool data to be erased. - First call the cursor on the screen if it is not being indicated on the NEXT display. Press the SPARE T ERASE menu key.
- Page 152 Return to Library Total erasure of registered tool data Press the menu selector key to display LAYOUT CANCEL. Press the LAYOUT CANCEL menu key. Î This will cause the display status of LAYOUT CANCEL to reverse. Specify −9999 with the numeric keys and then press the INPUT key. Î...
- Page 153 Return to Library WORK OFFSET Display Function: Setting zero-point offset for six workpiece coordinate systems (G54 to G59) for EIA/ISO programs. 5-2-1 Data display Displayed data D735S1012E Display data description Item Unit Data description Distance from the machine zero-point to the zero-point in G54 workpiece mm (inch) X, Y, Z coordinate system on each axis...
- Page 154 Return to Library Item Unit Data description Distance from the machine zero-point to the zero-point in G59 workpiece mm (inch) X, Y, Z coordinate system on each axis • degrees or 4, 5, 6 (Offset of workpiece zero-point) mm (inch) Shift amount of workpiece zero-point in each workpiece coordinate system.
- Page 155 Return to Library Shift amount of the workpiece coordinate systems (item •) Offset value of the external workpiece zero-point for shifting all the workpiece coordinate systems G54 to G59. Workpiece coordinate Workpiece coordinate Workpiece coordinate Workpiece coordinate system 1 system 2 system 3 system 4 Workpiece...
- Page 156 Return to Library (3) Place the cursor on the intended axis postion of the coordinate system where data setting is required. - Press the cursor key to call up the cursor on the CRT screen and move the cursor to the axis position of the coordinate system where the data is to be set.
- Page 157 Return to Library MACRO VARIABLE Display Function: This display allows macro variables to be set for the user macros. Remarks: - Two types of macro variables can be used: a) Common variables........Can be used for both the main program and the macro programs that are to be called up from the main program.
- Page 158 Return to Library 5-3-1 Data display Displayed data (COMMON VARIABLE, COMMON VARIABLE (CHECK)) Â % D735S1103E Display data description (COMMON VARIABLE, COMMON VARIABLE (CHECK)) Item Unit Data description Variable number • • Registered variable value DATA • • Page Current page/Total number of pages •...
- Page 159 Return to Library Data display (LOCAL VARIABLE, LOCAL VARIABLE (CHECK)) D735S1016E Display data description (LOCAL VARIABLE, LOCAL VARIABLE (CHECK)) Item Unit Data description Variable number • • Registered variable value DATA • • Nest Nesting number • • 5-1-2 Data registration COMMON VARIABLE and COMMON VARIABLE (CHECK) displays Only data of variables can be registered on the COMMON VARIABLE and COMMON VARIABLE (CHECK) displays.
- Page 160 Return to Library 5-1-3 Display operations COMMON VARIABLE and COMMON VARIABLE (CHECK) displays Pressing the INCRMENT INPUT menu key allows the entered data to be added to the current data. See the Section, TOOL DATA Display for further details. Use the Exp menu item to set data in exponential form. −...
- Page 161 Return to Library ADDITIONAL WPC Display Function: - By using this display, external coordinate data used for the MAZATROL program can be set. Remarks: - 10 sets of fundamental coordinates (A through K, except I) (workpiece coordinate system) can be set.
- Page 162 Return to Library Item Unit Data description Distance from the machine zero-point to the zero-point in workpiece X, Y, Z (4) (inch) coordinate system D on each axis • degrees (Offset of workpiece zero-point) th (4) Distance from the machine zero-point to the zero-point in workpiece X, Y, Z (4) (inch) coordinate system E on each axis...
- Page 163 Return to Library 5-1-4 Considerations to measurement Storing the tool tip position into the memory ADDITIONAL WPC display As with the WORK OFFSET display, the ADDITIONAL WPC display allows the tool tip position to be stored into the memory Refer to Subsection 5-2-2. Coordinate measurement If MMS or MDI•MMS operations are carried out for the fundamental coordinate unit that has an address set in ADD.
- Page 164 Return to Library Manual Measurement 5-5-1 Function overview Manual measurement allows both dimensional measurement and results display in the manual mode. With manual measurement, therefore, you can easily perform measurements without preparing a program when machining setup or dimensional measurement after machining has taken place.
- Page 165 Return to Library Alignment function For alignment with other than manual measurement capability, MDI MMS function is provided. This • is used to measure X-Y, X-Z, Y-Z plane coordinate values. If work origin is at the center of a hole, measurement is impossible.
- Page 166 Return to Library - Z coordinate at points A, B, and C must be identical. If Z coordinate value exceeds set parameter L12, alarm will be indicated, but measurement is possible. Parameter Point A Point B M3S055 Surface measurement For surface measurement, surface to be measured must be parallel to either of X-, Y- or Z-axes. Surface nomenclature If the selected surface is parallel to the X-axis, that surface is referred to as the X-axis surface.
- Page 167 Return to Library Example: JOG in X direction • X-axis surface is not selected. Distance component: λ z > λ y • Y-axis surface is selected M3S057 Angle selection Angular data for various axial surfaces should be as below. X-axis surface ..CCW angle from +Y-axis on Y-Z plane (150° in example below) Y-axis surface ..
- Page 168 Return to Library - Measurement direction (touch sensor movement direction) must be one of the axial directions (simultaneous two axes must not be used). - Measurement movement direction for measurement points A, B must be identical. Different directions will cause alarm. Straightness measurement (option) Selection of axial surface Selection of axial surface is the same as that of surface measurement.
- Page 169 Return to Library Distance, angle, parallelism, squaretness - Up to two items can be stored as data. Distance, angle, parallelism, and perpendicularity between two data items can be calculated and indicated. - For calculation of parallelism and perpendicularity, value will be indicated always with data 1 as base.
- Page 170 Return to Library Item Unit Data description Denotes the difference in angle between two surfaces. deg. No data will be displayed if the distance is not derived from two sets of ANGLE measurement results. Degree of parallelism/perpendicularity in “mm”, and the difference in the angles of two planes in “%”.
- Page 171 Return to Library Table C Distance calculation pattern Conditions Circle and circle Circle and Z-axis surface None Circle and degree of straightness with respect to the Z- axis surface Circle and X- or Y-axis surface Each surface must be parallel to the Z-axis (within the Circle and the degree of straightness with respect to the range of parameter L13).
- Page 172 Return to Library 5-1-6 Measuring procedure Measuring procedure is outlined below. JOG mode (MDI: During Straightness Manual pulse, jog, rapid feed mode measurement) Touch sensor moved Contact made Measuring pattern close to measurement by JOG selection by menu point by manual feed Repetition Circle measurement Manual...
- Page 173 Return to Library Surface measurement Manual [1st point] Manual [2nd point] Surface measurement M3S064 Press the SURFACE MEASURE menu key. Î This displays the message FIRST POINT MEASURING and reverses the display status of the menu item. - The corresponding “Help” window can be displayed by selecting through the “Window” item on the menu bar.
- Page 174 Return to Library Measure the starting point using the jog feed function. Î This displays the coordinates of the starting point of measurement and then displays the message REQUEST FINAL POINT. Measure the ending point using the jog feed function. Î...
- Page 175 Return to Library Two-point measurement Manual Manual First point Second point Two-point measurement M3S067 Press the 2 POINT MEASURE menu key. Î This displays the message FIRST POINT MEASURING and reverses the display status of the menu item. - The corresponding “Help” window can be displayed by selecting through the “Window” item on the menu bar.
- Page 176 Return to Library Measurement result clearing Masurement results can be cleared. Press the CLEAR RESULT menu key. Î This displays the message CLEAR MEASURING RESULT No.?. Input the identification number (1, 2, or 0) of the measurement results to be cleared, and then press the INPUT key.
- Page 177 Return to Library Incremental data input The data to be written can be input in incremental form. Press the INCRMENT INPUT menu key. Î This displays the message LENGTH TO ADD? and reverses the display status of the menu item. Input the data to be added, and press the INPUT key.
- Page 178 Return to Library 5-1-8 Graph of straightness data (option) All measurement results will be indicated by numeric values on the MEASURE display. In addition, straightness data will be graphically shown on a line graph. The measurement results and graph can be copied. Calling up the STRAIGHTNESS GRAPH display Press the STRAIGHT GRAPH menu key on the basic menu of the MEASURE display.
- Page 179 Return to Library Menu function MEASURE Direct return from the graph to the MEASURE display. PARALLEL PERPNDLR When surface, straightness measurement data in “1:”, and straightness measurement data in “2:” and parallelism and squareness are calculable between these two data, data “1:” is taken as reference on horizontal axis, on which graph for data “2:”...
- Page 180 Return to Library SPINDLE LOAD GRAPHIC DISPLAY Display Function: Displaying the changes in the speed and load of the spindle. 5-6-1 Data display Displayed data D735S1020E Display data description Item Unit Data description Tool number Numbers of the tools mounted on the spindle •...
- Page 181 Return to Library 5-1-2 Displaying spindle load data Start the sampling of the spindle load data. - Select the POSITION display, press the WINDOW key and select “Spindle Load” through “File” on the menu bar. Select the display SPINDLE LOAD GRAPHIC DISPLAY. Note 1: To stop sampling, press the WINDOW key once again first.
- Page 182 Return to Library Displaying the data of only a specific tool in enlarged form Data of only a specific tool can be displayed in enlarged form. Press the CHANGE TOOL menu key. Î The display of the menu item will be reversed and the message TOOL No. <CURSOR, INPUT>? displayed.
- Page 183 Return to Library MACHINING NAVIGATION - RESULT Display Function: The machining time and spindle output data are listed for each tool according to the results of actual machine operation. 5-7-1 Data display Displayed data with normal display of TOOL DISTINCT menu item D735S1021E 5-41...
- Page 184 Return to Library Displayed data with reverse display of TOOL DISTINCT menu item D735S1022E Display data description Item Unit Data description Work number of the machining program WNo. a b ( c ) WNo. • • a : Work number b : Program type (MAZATROL or EIA/ISO) c : Program name H/M/S...
- Page 185 Return to Library Item Unit Data description Unit number UNo. • • Unit name UNIT • • SNo. Tool sequence number • • TIME RATIO Ratio of machining time for each tool sequence • –1 Spindle speed specified in the tool sequence •...
- Page 186 Return to Library - Tool-specific display mode In this display mode, which can be selected and canceled by pressing the TOOL DISTINCT menu key, data of a specific tool sequence listed up in the total display mode can be selectively displayed in further detail.
- Page 187 Return to Library Using the cursor keys, position the cursor on the desired tool sequence number. Î The black triangle will move correspondingly with the cursor so that the ratio of the machining time of the specific tool sequence to the total machining time can be visually checked.
- Page 188 Return to Library - NOTE - 5-46...
- Page 189 Return to Library DISPLAYS RELATED TO PROGRAM CREATION PROGRAM Display Refer to the Programming Manual (MAZATROL) when creating MAZATROL programs or the Programming Manual (EIA/ISO) when creating EIA/ISO programs. An example of display presentation (for MAZATROL programming) D735S1023E TOOL PATH CHECK Display Function: This display is used to display the machining shapes and the tool-tip path that have been defined by the machining program.
- Page 190 Return to Library 6-2-1 Data display Displayed data D735S1024E Display data description Item Unit Data description Machining shape that has been defined by the program (For point-machining, (Shape) • this data is displayed with a purple line. For line- or face-machining, this data is displayed with a green line.) •...
- Page 191 Return to Library 6-1-2 Displaying machining shape Press the PART SHAPE menu key. Î This will cause the display status of PART SHAPE to reverse and the machining shapes that have been defined by the program to be displayed continuously. - Point-machining shapes will each be displayed with a purple line, and line- or face- machining shapes will each be displayed with a green line.
- Page 192 Return to Library 6-1-4 Restarting tool path check Tool path checks can be carried out in the middle of the program. Press the menu selector key. Press the PATH RESTART menu key. Î The display status of the menu will then reverse and a restart data setting window will be opened.
- Page 193 Return to Library Tool-path display using special interpolation functions such as those for spiral-cutting operations do not correspond completely with actual tool movements. 6-1-7 Solid Mode The tool path specified in a MAZATROL program can be checked in a quasi-actual machining image as shown below by executing the solid-model display function, so that a cutting area error and other abnormalities can be detected in an earlier stage and the test cutting time can be saved correspondingly.
- Page 194 Return to Library Operation Select the solid mode. - Press the SOLID MODE menu key on the TOOL PATH CHECK display. D735S1026E...
- Page 195 Return to Library Î A solid-model display will appear as shown in the example below. D735S1027E - The rectangular parallelopiped that has been set to the appropriate size according to the selected MAZATROL program is displayed as the material to be machined. Note 1: Selecting the SOLID MODE menu function for an EIA/ISO program will cause an alarm.
- Page 196 Return to Library Machine origin –200 Machining area –150 BASE Machine origin Machining area –100 BASE D735S1029 Change the coordinates of BASE and the dimensions of SIZE as required by placing the cursor on the desired text box first and then entering the corresponding value. Click the OK button with the mouse, and the window will be closed.
- Page 197 Return to Library - The following display environment edit function can be executed from the above window: Click an item the display color of which is to be changed: MATERIAL, TOOL, SURF. (machining surface), BACK. (background) or TAP. Change the color indicated in the box next to the item name by selecting the new color from the palette.
- Page 198 Return to Library Rotation of the solid Press the ROTATION menu key and, with the menu item displayed in reverse, use the cursor keys to rotate the solid given on the display. (See the explanatory table given below under Note 2 for the function of the cursor keys.) Movement of the solid Press the MOVE menu key and, with the menu item displayed in reverse, use the cursor keys...
- Page 199 Return to Library - Function of the cursor keys for ZOOM IN/OUT, ROTATION and MOVE functions Current display of the solid Relationship between cursor keys and menu functions Selected function ZOOM IN/OUT ROTATION MOVE Cursor Enlargement Right turn around horizontal axis Upward Reduction Left turn around horizontal axis...
- Page 200 Return to Library Terminate the solid-mode display. - Press the SOLID MODE menu key once again. Î Any operation in the solid mode (tool path drawing, display modification) will be forcibly terminated and the display mode will be reset to the normal mode. Solid mode display for each unit type of MAZATROL programs The solid mode display for tool path check can only be selected for an MAZATROL program currently designated on the PROGRAM display (as the main program).
- Page 201 Return to Library Unit Tool Display Remarks RGH CBOR CTR-DR Refer to DRILLING unit for tool image displayed. • DRILL • • E-MILL Tool image displayed • CHF-C Refer to DRILLING unit for tool image displayed. • RGH BCB CTR-DR Refer to DRILLING unit for tool image displayed.
- Page 202 Return to Library Unit Tool Display Remarks CHF-C • • CHP VAC No tool image displayed. • Tool image displayed • Machining surface in the selected color (Default: light blue) BORE T1 CTR-DR Refer to DRILLING unit for tool image displayed. •...
- Page 203 Return to Library Unit Tool Display Remarks E-MILL Tool image displayed • (Tornado cycle) Chamfering section is only presented as a rectangular cutting. Tool • Top view • Sectional view Tapping and reaming tools are presented like an end-milling tool as shown above. •...
- Page 204 Return to Library Line machining unit •: Almost real image of machining and tool Unit Tool Display Remarks LINE CTR E-MILL Refer to RGH CBOR unit for tool image displayed. • LINE RGT E-MILL • • LINE LFT E-MILL • •...
- Page 205 Return to Library Special unit - M-CODE unit: Ignored. - SUB PRO unit (for call of a MAZATROL program): The tool path is drawn for the SUB PRO unit in the solid mode according to the machining units (Point, Line, Face) designated in the MAZATROL subprogram. - SUB PRO unit (for call of an EIA/ISO program): The last tool in the flow of the main program is used further for the solid display of the whole EIA/ISO subprogram.
- Page 206 Return to Library Even a section not covered by a tool image display is surely cleared in the flow of machining as shown below. è D735S1039 This section is also cleared simultaneously with the feed motion of the displayed tool. •...
- Page 207 Return to Library SHAPE CHECK Display Function: The machining shapes that have been defined using the machining program are displayed. (The machining shapes between one WPC unit and the next WPC unit are displayed.) Remarks: - This display can be selected when the cursor is at the unit position during MAZATROL program creation.
- Page 208 Return to Library Display data description Item Unit Data description Machining shape that has been defined by the program (Shape) (For point-machining, this data is displayed with a purple line. For line- or face- • • machining, this data is displayed with a green line.) mm (inch) Display limit (automatically determined according to the machining shape) •...
- Page 209 Return to Library 6-1-3 Other menu functions If the PLANE CHANGE menu key is pressed, it becomes possible to select the plane or 3-D view on which machining shapes are to be displayed. For details of the selecting procedure, see the Subsection 4-2-3 Plane select that is given in Section 4-2 TRACE Display. If the plane select is not carried out, the machining shape available on the XY plane will be displayed.
- Page 210 Return to Library PLANE CHECK Window Function: The machining shapes of the program unit are displayed. Remarks: - This window can be selected when the cursor is on the shape sequence line during MAZATROL program creation. - The machining shapes are displayed on the XY plane. 6-4-1 Data display Displayed data...
- Page 211 Return to Library 6-1-2 Displaying machining shape Press the PLANE CHECK menu key to display the PLANE CHECK window. Continuous display Operate the cursor keys to move the foucus onto the button CONT. in the window and press the INPUT key. Î...
- Page 212 Return to Library 6-5-1 Data display Displayed data D735S1042E Display data description Item Unit Data description (Sectional shape) Point-machining sectional shape • • Scaling factor for graphic display (automatically determined according to the mm (inch) • type of machining shape) Work number of the program under which the sectional check is to be made WNo.
- Page 213 Return to Library 6-1-2 Displaying sectional shapes Press the SECTION CHECK menu key to display the SECTION CHECK window. Continuous display Operate the cursor keys to move the foucus onto the button CONT. in the window and press the INPUT key. - The point-machining sectional shapes that have been defined in the line where the cursor is blinking on the PROGRAM display will be indicated continuously.
- Page 214 Return to Library PROGRAM FILE Display Function: Displaying the work numbers and other data of the programs pre-registered in the NC unit Remarks: The following operations can be carried out for the pre-registered programs: - Name assignment - Work number change - Erasure - Program copy - Converting MAZATROL programs to EIA/ISO programs (option)
- Page 215 Return to Library Display data description Item Unit Data description - Work number of a pre-registered program, and program type identification (MAZATROL programs or EIA/ISO programs) WORK No. • • M: MAZATROL program E: EIA/ISO program Number of blocks in the registered program SIZE •...
- Page 216 Return to Library 6-1-3 Work number change A work number is set during creation of a program. The work number of each program pre- registered in the NC unit can be changed as required. Place the cursor on the work No. to be changed. Press the PROGRAM RENUMBER menu key.
- Page 217 Return to Library 6-1-5 Program copy This operation enables the previously registered programs within the NC unit to be copied. Use this function to newly create the similar programs as those which have been registered. Move the cursor to the line where the work number of the program to be copied is displayed. - The cursor can be set at any of the items present on the line where the intended work number is displayed.
- Page 218 Return to Library Press the PART SHAPE menu key. - Press the PART SHAPE menu key again if the shape drawing window is to be cleared. Î PART SHAPE will then be displayed in the normal-display status and the shape drawing window will close.
- Page 219 Return to Library 6-1-10 Program transfer Use the following procedure to transfer a program from one storage area to another: Press the PROGRAM TRANSFER menu key. Î The display status of PROGRAM TRANSFER changes to reverse and the following window appears: Specify the work number of the program to be transferred and select the destination area.
- Page 220 Return to Library Prohibition of selected-program call Display of the contents of the selected program is prohibited. The alarm 402 ILLEGAL NUMBER INPUT will occur if an attempt is made to carry out for the selected program the operations listed in the table below. Type of display Prohibited item PROGRAM display...
- Page 221 Return to Library PROCESS CONTROL Display Function: The logical linking status of processes within the program and the configurations of the subprograms within the processes are displayed. Remarks: Subprograms that are called up from the EIA/ISO programs will not be displayed on this display. 6-7-1 Data display Displayed data...
- Page 222 Return to Library Item Unit Data description Work number of the subprogram (Nesting 4) SUB 4 • • Work number of the subprogram (Nesting 5) SUB 5 • • SUB 6 Work number of the subprogram (Nesting 6) • • SUB 7 Work number of the subprogram (Nesting 7) •...
- Page 223 Return to Library PROGRAM LAYOUT Display Function: - The tools to be used in the processes of the MAZATROL program are displayed in the order of machining. - This display can be used to edit a tool priority number and to write the data into the program. Remarks: - For both multi-workpiece machining and subprogram looping, only one time of program data is displayed.
- Page 224 Return to Library Display data description Item Unit Data description Order of machining • • PRI. No. Tool priority number • • Tool sequence number SNo. • • Tool name TOOL • • mm (inch) Nominal diameter of the tool NOM-φ...
- Page 225 Return to Library 6-1-5 Priority number movement A tool priority number can be moved. Move the cursor to the PRI. No. item to be moved. Press the PRI. No. MOVE menu key. Input a destination tool priority number , and press the INPUT key. Î...
- Page 226 Return to Library * If, in procedural step (1), the cursor is set to a position in which a priority number has not been designated, only the tool sequence priority number at the cursor position will move. Example: NOM- φ NOM- φ...
- Page 227 Return to Library Data that has been set in the PROGRAM LAYOUT display can be written into the program. After editing, however, the program write operation described below must be carried out to incorporate the data into the program. Press the PROGRAM WRITE menu key. Î...
- Page 228 Return to Library MACHINING NAVIGATION - PREDICT Display Function: The machining time and spindle output data are listed for each tool according to the estimates made by the checking operation on the TOOL PATH CHECK display. The machining time can therefore be reduced effectively.
- Page 229 Return to Library Displayed data with reverse display of TOOL DISTINCT menu item  5 D735S1047E Display data description Itme Unit Data description Work number of the machining program currently selected on the PROGRAM display. WNo. a b ( c ) WNo.
- Page 230 Return to Library Itme Unit Data description Not displayed (used only for the MACHINING NAVIGATION - RESULT PEAK • display) Work number of the program WNo. • • Unit number UNo. • • Unit name UNIT • • Tool sequence number SNo.
- Page 231 Return to Library ← \ nm64mdata\eng\cspmat.txt F ile name [Material-1] Name=FC250 ← W orkpiece material Coeff-1=38 Coeff-2=568 Coeff-3=73 Coeff-4=139 Description of the coefficients used in the calculation of the average output for a workpiece made of FC250. Do not change the values inadvertently. Coeff-5=105 Coeff-6=295 Coeff-7=1500...
- Page 232 Return to Library 6-1-3 Display modes Outline This display has the following two display modes: - Total display mode The display is always made in this mode when the MACHINING NAVIGATION - PREDICT display is selected. In this display mode, estimated machining time and average spindle output are listed for each tool sequence in addition to the general information about execution of the program.
- Page 233 Return to Library Press a cursor key. Î The cursor will appear in the “TNo.” column. - A black triangle (•) will be displayed under the graph “RATIO OF MACHINING TIME” to indicate the item of the tool sequence currently selected by the cursor, as shown in the display example below.
- Page 234 Return to Library EXAMPLE window In the tool-specific display mode, the MAZAK-recommended effective tools are presented in a window for the selected tool sequence. Press the EXAMPLE menu key. Î The display of the menu item will be reversed and the window for the recommended effective tools will be displayed.
- Page 235 Return to Library Note: It is possible to edit the four cutting conditions displayed in the CUTTING COND. display area (C-SP, FR, DEP-Z and WID-R), of which, however, only those corresponding to the selected tool sequence are subjected to the edition. Refer to the Programming Manual - MAZATROL - for the description of the data items of the tool sequence.
- Page 236 Return to Library - NOTE - 6-48...
- Page 237 Return to Library DISPLAYS RELATED TO TOOLS TOOL DATA Display Function: - Registering magazine-mounted tools and setting tool shape data and the data required for management of the tools Remarks: - Tool materials data that has been set on this display is used as learning data relating to cutting conditions.
- Page 238 Return to Library The operation of the cursor keys and page keys differs as follows according to the selected area: TOOL LIST area CONTENTS area Cursor keys Selection of a tool data line Selection of a data item Page keys Selection of a page of list Selection of a tool data line on the list page Displayed data...
- Page 239 Return to Library Item Unit Data description Group number of the tool (the same group number is assigned to all tools that • GROUP No. • are the same in both shape and dimensions.) Tool ID number ID No. • •...
- Page 240 Return to Library The shape data necessary to perform actual machining and the data necessary for management purposes must be input for each of the displayed tools. These data are: ACT-φ, LENGTH, LENG COMP., AUXIL., THRUST F, HORSE PW, LIFE TIME, CUT TIME , MAT. and MAX. ROT. However, there are data that do not need to be input according to the type of tool.
- Page 241 Return to Library - In the example given above for an end-mill, skip the cursor to the next item by pressing the key because cutting-end position compensation is not necessary. - The value 0 is preset to each of the LENG COMP., THRUST F., HORSE PW, LIFE TIME, CUT TIME and MAX.
- Page 242 Return to Library (12) Move the cursor to the MAT. item, and press the menu key corresponding to the type of material to be set. - If a milling tool that has been registered on the TOOL FILE display is registered here, the corresponding type of material set previously on that display will be auto-set.
- Page 243 Return to Library Note 2: The maximum rotational speed data cannot be set for TOUCH SENSOR and CHIP VACUUM. Note: Data that has been set during steps (13) and (14) above is valid only for the machine models equipped with AFC. The operations described above are not required for the machine models of standard specifications.
- Page 244 Return to Library 7-1-4 Registering the tools to be used Proceed as follows to register on the TOOL DATA display the tools to be used: Press the Tab key as required to select the left column (TOOL LIST) beforehand, and press a cursor key to call up the cursor.
- Page 245 Return to Library - Menu (c) refers to the intra-magazine interference data as follows: ORDINARY DIAMETER ..Diameter of a tool which completely fits into the pocket. LARGE L......Tool which interferes with both next tools in the pocket. MAG DIR+ +......Tool that interferes with the tool of a larger pocket number. MAG DIR–...
- Page 246 Return to Library Machine zero-point Distance from the machine zero- point to the current position of Distance from the the machine machine zero- Manual axis point to the table movement surface (constant) Current position of the machine Tool length Distance from Reference block the table surface or workpiece...
- Page 247 Return to Library Press the TOOL SEARCH menu key. Î The following menu will be displayed ENDMILL FACEMILL CHAMFER BALL OTHER TOUCH >>> CUTTER ENDMILL TOOL SENSOR - Pressing the menu key >>> changes the above menu over to the following menu: CENTER DRILL BACKSPOT...
- Page 248 Return to Library Select TNo. 2. Press the EDIT menu key. Press the TOOLDATA ERASE menu key. Î This will cause the display status of TOOLDATA ERASE to reverse. Press the INPUT key. Î Selected tool data will be erased. TOOLNAME ORDER (displayed only for machines with a random ATC feature) For machines having a random ATC feature, use this menu function if the tool data previously registered on the TOOL DATA display is to be rearranged in order of tool name.
- Page 249 Return to Library Using the cursor keys, move the cursor in the TOOL LIST area onto the line of a drill for which the threshold is to be set. Press the BORDER VALUE menu key. Î The display of the menu item will be reversed and the following dialogue box will appear: Using the cursor keys, position the cursor on the text box “TORQUE”.
- Page 250 Return to Library Input tool length offset data using the numeric keys, and press the INPUT key. - When the tool length offset data is set, the No. item on the right will become blank to indicate that the item has become invalid. - For the current tool on the spindle only, tool length offset data can be set using the LENG- OFS TEACH menu function.
- Page 251 Return to Library Note 2: When the tool for which the offset data has been set on this display is to be used during execution of the program, the offset data (or offset number data) that has been set on this display will govern even if another offset data number has been designated in the program.
- Page 252 Return to Library 7-1-8 Setting tool group numbers If a group number is set for the tools that are to be used during execution of the program, the next spare tool to be used will be auto-selected from tools of the same group number. Selection of spare tools As listed below, two methods are available to select spare tools.
- Page 253 Return to Library 7-1-9 Manual measurement of tool lengths (Setting tool length offset data using the LENG- OFS TEACH menu function) The LENG-OFS TEACH menu function can be used to set tool length data in the LENG CORR. Manually move the axes, and bring the nose of the tool into contact with the top of either a reference block or a workpiece whose height is predetermined.
- Page 254 Return to Library Press the INPUT key. “DSBL” for indication of an invalid tool Machine action Only in the following cases, tools designated as invalid (DSBL) on the TOOL DATA display are regarded as invalid tools. during automatic operation during tool path check during “tool layout”...
- Page 255 Return to Library Tool path check is performed The machine action differs as follows between tool path check using a MAZATROL program and tool path check using an EIA/ISO program: During tool path check using a MAZATROL program Invalid tools are not selected. If an alternative, usable tool of the same type is not present, a tool path will be drawn in the absence of a tool (diameter offsetting will use the tool nominal diameter data existing in the program).
- Page 256 Return to Library Tool number scheme (User parameter F92, bit 4 = 1) When the tool of the selected tool number is invalid: (a) If a group number has been set, a spare tool search will be made using that group number.
- Page 257 Return to Library 7-1-12 Tool length listing window Outline The tool length listing window is provided on the TOOL DATA display in order for the operator to easily enter data of items LENGTH, LENG COMP. and ACT-φ for multiple tools without having to select each time the particular tool for the CONTENTS area.
- Page 258 Return to Library TOOL FILE Display Function: - This display is used when registering the data of the milling tools to be used, such as end-mills, face-mills, chamfering cutters, ball end-mills, etc. Remarks: - The TOOL FILE display is divide d into the following four displays according to the type of milling tool to be used: 1.
- Page 259 Return to Library 7-1-1 Data display Displayed data of the displays for end-mills and ball end-mills  #  $  &  '  (  #  $  &  '  (  * D735S1050E Displayed data of the displays for face-mills Â...
- Page 260 Return to Library Display data of the display for chamfering cutters  #  $  %  &  (  )  #  $  %  &  (  )  * D735S1052E Display data description Item Unit Data description...
- Page 261 Return to Library 7-1-2 Registering milling tool data When registering milling tools on the TOOL FILE display, the types of data to be set differ according to the types of tools to be used. The setting procedure, however, is the same for all types of data except chamfering cutters.
- Page 262 Return to Library Î The input value will then be displayed under NOM-φ, and the cursor will move to the right side of that value. NOM-φ MAT. DEPTH TEETH • - The following menu for assigning tool ID codes will be presented in the menu display area: HEAVY >>>...
- Page 263 Return to Library (10) Using the numeric keys, specify the maximum depth of cut that can be machined during one cutting operation (i.e., the length of the cutting edge of the end-mill). Then, press the INPUT key. - In the example given, specify “30” and press the INPUT key. (11) Move the cursor to the TEETH item.
- Page 264 Return to Library Press the cursor key to move the cursor to the position of the No. item to be registered. NOM-φ MIN-φ MAT. TEETH ANG. • Move the cursor to this position • - The cursor can be moved only to the lines of numbers which have been registered and the next line.
- Page 265 Return to Library (10) Move the cursor to the ANG. item. (11) Input the nose angle of the tool to be registered, and press the INPUT key. - In the example shown above, specify “45” and then press the INPUT key. NOM-φ...
- Page 266 Return to Library TOOL OFFSET Display Function: This display is used when setting the amount of tool-diameter or tool-position compensation of each tool to be used for an EIA/ISO program. Remarks: Current position on each axis can be set. 7-3-1 Data display Type of tool offset differs according to the particular machine model (there are two types of tool offset, type A and type B), and data that will be displayed also differs according to the selected...
- Page 267 Return to Library Displayed data of type B Â # Â $ Â % Â # Â & Â ' D735S1054E Display data description for type B Item Unit Data description Tool offset number for the registered offset amount • •...
- Page 268 Return to Library Automatic setting procedure using the TEACH function Using the TEACH function of the display, tool-length compensation data can be automatically input to the OFFSET item of the TOOL OFFSET (type A) display or the TOOL LENGTH GEOMETRY item of the TOOL OFFSET (type B) display.
- Page 269 Return to Library 7-1-3 Setting the current position The current position of the tool nose in the workpiece coordinate system can be set while the POSITION window remains on the TOOL OFFSET display. See Section 2-4 Window, for further details of the POSITION window. The procedure for setting the current position of each axis is described below.
- Page 270 Return to Library Fully automatic tool length measurement - Operating procedure Select the TOOL OFFSET display. Set the MDI mode. Î This displays an MDI window. Press the T MSR AUTO menu key. Î This reverses the display status of the menu item to make the right-hand half of the display into the setting/display area of tool length measurement data.
- Page 271 Return to Library Press the INPUT key - This displays measurement M- and T-codes in the MDI window and causes the corresponding offset number(s) on the left half of the display to reverse in red. D735S1056E While the display of the menu item shown previously at step (3) remains in reverse form, steps (4) to (8) can be repeated for up to a maximum of 13 tools.
- Page 272 Return to Library status of the menu item. If an offset number is unset, no measurement M-codes will be displayed in the MDI window. Press the CYCLE START button to perform the measurement operation. - Use semi-automatic tool length measure-ment if, as shown below, tool interference is to be considered for beforehand.
- Page 273 Return to Library DISPLAYS RELATED TO PARAMETERS CUTTING CONDITION (W.-MAT./T.-MAT.) Display Function: Registering the materials types of workpieces and tools that are to be selected for automatic setting of cutting conditions on the PROGRAM (MAZATROL) display and the TOOL FILE display Remarks: - Data that has been registered on this display can be used only for a MAZATROL program.
- Page 274 Return to Library 8-1-2 Registering data The CUTTING CONDITION (W.-MAT./T.-MAT.) display allows the names of the materials of workpieces and tools to be registered using character strings of alphabetic characters and arabic numerals. Display the cursor by pressing the cursor key. Move the cursor to any of the workpiece materials data items from MAT.1 to MAT.16 or the tool materials data items from MAT.1 to MAT.8.
- Page 275 Return to Library 8-1-3 Read and Write of text file The workpiece and tool material names (W.-MAT. and T.-MAT.) in the cutting conditions can be taken in and out as a text file of the hard disk. Use the item “File” on the menu bar to perform these operations.
- Page 276 Return to Library Example 1: • m W ORK • n “S45C” is registered as workpiece material No. 1. 1,S45C 2,... File Note 1: The material name can consist of a maximum of eight half-size characters (or four normal-size characters). Note 2: The character string of the material name must not begin or end with a half-size null code.
- Page 277 CUTTING CONDITION (FR) display - Data that has been registered on this display is used only for MAZATROL programs. - Data recommended by Yamazaki Mazak is pre-registered prior to shipping of the machine. The registered data can be modified as required.
- Page 278 Return to Library CUTTING CONDITION (FR) display ‡ E ‡ @ ‡ B ‡ A ‡ D D735S1083E Display data description Item Unit Data description Tool name Name (type) of the currently selected tool Name of the material of the workpiece W.-MAT.
- Page 279 Return to Library 8-2-2 Data registration The following data can be registered for each tool on the CUTTING CONDITION display: Surface velocities for each workpiece material type registered on the CUTTING CONDITION (W.-MAT./T.-MAT) display Feed rates for each workpiece material type registered on the CUTTING CONDITION (W.- MAT./T.-MAT) display Cutting conditions data differs according to the selected type of milling tool, type of workpiece material, and type of tool material.
- Page 280 Return to Library CARBID BALANCE MAT. Using the cursor keys, move the cursor to the HSS column of the drilling tool for the workpiece material “FC”. (Use the page keys to enter the FR data for other types of tool.) DRILL T.-MAT.
- Page 281 Return to Library Data Data of various user parameters Note 1: For further details, see the Prameter List. Note 2: Confirm the contents of parameters before changing them.
- Page 282 Return to Library MACHINE PARAMETER Display Function: Registering and displaying machine parameters 8-4-1 Data display Displayed data ‡ B ‡ @ ‡ A ‡ A ‡ A ‡ @ ‡ A ‡ A ‡ A D735S1105E Display data description Item Unit Data description Address...
- Page 283 Return to Library - NOTE - 8-11...
- Page 284 Return to Library DISPLAY RELATED TO DATA STORAGE DATA I/O Display Function: This display is used to transfer programs or other types of data between the NC unit and an external unit. 9-1-1 Data display Displayed data  %  % Â...
- Page 285 Return to Library 9-1-2 DATA I/O operations (CARD) The following four data input/output operations can be executed using a memory card. Loading The program data or other types of data prestored on a memory card are registered into the NC unit. Saving The program data or other types of data pre-registered in the NC unit are stored onto a memory card.
- Page 286 Return to Library Deleting the directory To delete a directory (with all the files thereunder) on the memory card, proceed as follows: (1) Press the DIR. DELETE menu key. Î DIR. DELETE will change to a reverse-display status and the following window will appear.
- Page 287 Return to Library - The highlighted-display status of the data that has been transferred will be cleared. The same data will be displayed in the (NC) column. - After data transfer, the reverse-display status of START will be cleared. Note 1: You can select using a parameter whether loading of a program whose work number is the same as that of a program pre-registered within the NC unit, is to be enabled.
- Page 288 Return to Library Directorying Press the CARD menu key. Press the CARD CONTENT menu key. Î DIR will be displayed on the I/O data item. Press the START menu key. Î START will change into a reverse-display status, and what type of data is stored on the memory card will be displayed in the (CARD) column on the display.
- Page 289 The operating procedure of each operation listed above is described below. The following description assumes that a cassette tape deck or a MAZAK microdisk unit has already been connected to the NC unit and that cassette tape or microdisk setting is also completed.
- Page 290 Return to Library Press the START menu key. Î START will change into a reverse-display status and data transfer will begin. - The display color will change at the position where the data being transferred is displayed. - The highlighted-display status of the data that has been transferred will be cleared. The same data will be displayed in the (NC) column.
- Page 291 Return to Library Press the START menu key. Î START will change to a reverse-display status and data transfer will begin. - The display color will change to purple at the position where the data being transferred is displayed. - The data that has been transferred will change to a normal display status and the same data will be displayed in the (CMT) column.
- Page 292 Return to Library Directorying Press the CMT I/O menu key. Press the CMT CONTENTS menu key. Î DIR will be displayed on the I/O data item. Press the START menu key. Î START will change into a reverse-display status, and what type of data is stored on the cassette tape (CMT) or the microdisk will be displayed in the (CMT) column on the display.
- Page 293 The operating procedure for the functions listed above is described below. The following description assumes that a paper tape reader/puncher or a MAZAK microdisk unit has already been connected to the NC unit and that paper tape or microdisk setting is also completed.
- Page 294 Return to Library - The display color will change to purple at the position in which the data being transferred is displayed. - After data transfer, the reverse-display status of START will be cleared. Note: The precautions described in Notes 1, 2, 4 and 5 in “1. Loading” of 9-1-3 DATA I/O operations (CMT) are valid for this loading operation.
- Page 295 Return to Library Comparing Press the TAPE I/O menu key. Press the COMPARE NC = TAPE menu key. Î COMPARE will be displayed on the I/O mode item. Select the data to be compared. - See the description of procedural step (3) of “1. Loading”. Press the START menu key.
- Page 296 Return to Library - All punching - Comparing - All comparing Tape format The name of the program transferred to or from a tape must be designated as follows: Set the control-out code “(” after the number with O, then set the program name and the control-in code “)”, in that order.
- Page 297 Return to Library 9-1-5 DATA I/O operations (FLOPPY) The following four data input/output operations can be executed using a floppy disk. Loading The program data or other types of data prestored on a floppy disk are registered into the NC unit.
- Page 298 Return to Library (2) Key in the name of the directory to be deleted and press the INPUT key. - Use the alphabetic and numeric keys to input the name. Note: All the files stored under the specified directory will be deleted by the above operation. Loading Press the FLOPPY menu key.
- Page 299 Return to Library Saving Press the FLOPPY menu key. Press the SAVE NC → FD menu key. Î SAVE will be displayed on the I/O mode item. Select the data to be transferred. - The data input procedure is the same as that of LOAD. Input the data in the (NC) column. (See procedural step (3) of “3.
- Page 300 Return to Library machines are transferred to the NC unit of this machine. Saving Non-program data or programs pre-registered within the NC unit of this machine are transferred to a host CPU or the NC unit of other machines. The operating procedure for the operations listed above is described below. The following description assumes that the NC unit of this machine has already been connected to the NC unit of other machines or a host CPU.
- Page 301 Return to Library displayed. - The data that has been transferred will change to a normal display status and the same data will be displayed in the (NC) column. - After data transfer, the reverse-display status of START will be cleared. Note: All the precautions in Notes in “1.
- Page 302 Return to Library presented in a window. (2) Set the parameters as required. - Refer to the Parameter List for details of the parameters. (3) Press the INPUT key or click OK in the window. The reverse-display status of PARAM. will be cleared and the window will disappear. Setting of detailed parameters (1) Press the PARAM.
- Page 303 Return to Library 9-1-7 DATA I/O operations (HARD DISK) The following three data input/output operations can be executed using the hard disk. Loading The program data or other types of data prestored on the hard disk are registered into the NC unit.
- Page 304 Return to Library Deleting the directory To delete a directory (with all the files thereunder) on the hard disk, proceed as follows: (1) Press the DIR. DELETE menu key. Î DIR. DELETE will change to a reverse-display status and the following window will appear.
- Page 305 Return to Library Press the START menu key. Î START will change into a reverse-display status and data transfer will begin. - The display color will change at the position where the data being transferred is displayed. - The highlighted-display status of the data that has been transferred will be cleared. The same data will be displayed in the (NC) column.
- Page 306 Return to Library Program Transfer from the Host PC to the Memory Card 9-2-1 Outline This section explains how to transfer machining programs, under an Ethernet-based network environment, from the host PC to the memory card inserted into the front slot on the M640 operating panel.
- Page 307 Return to Library Select the HD-operating program storage folder by clicking “MC_Direct Mode Programs”. D735S1107E Click the right-hand button of the mouse on “MC_Direct Mode Programs” to display the pop- up menu. D735S1108E By clicking the left button of the mouse, select “Sharing ...” from the pop-up menu to display the Properties dialogue box for the sharing.
- Page 308 Return to Library Set data as follows in the Sharing Properties dialogue box: D735S1109E - Sharing.....Select “Shared As”. - Share Name ..Leave the automatically set name (MC_DIRECT MO) as it is. - Access Type ..Select “Full”. - Passwords ..Skip setting. Note: Although any share name can be entered, it is recommended for users unfamiliar with Windows to use the automatically set name.
- Page 309 Return to Library Copying program files from the host PC into the HD-operating program storage folder The Windows Explorer allows program files within the host PC to be copied into the HD-operating program storage folder of the M640. This section introduces the procedure for accessing from a Windows95-containing host PC the M640 HD-operating program storage folder that was modified into a sharable folder as described in Section 1 above and then copying an existing program file from any folder within the host PC.
- Page 310 Return to Library Position the mouse pointer on the desired program in the displayed folder, press and hold down the left button of the mouse, move the pointer into the Contents area of the HD- operating program storage folder, as displayed in Step (1) above, on the Windows Explorer, and release the mouse button.
- Page 311 Return to Library D735S1113E Copying program files from the HD-operating program storage folder onto the memory card The procedure is as follows: Press the DATA I/O menu key. ress the CARD menu key. Press the HD AREA menu key. Î HD AREA will change to a reverse-display status to indicate that data input/output operations can be performed on the HD-operating program storage folder.
- Page 312 Return to Library Specify the program(s) to be transferred. Press the START menu key. Î START will change to a reverse-display status to indicate that transfer of the program has been started. - The reverse-display status of START will be cleared upon completion of the program transfer.
- Page 313 Return to Library - NOTE - 9-30...
- Page 314 MONITOR*, SPINDLE MONITOR*, HARDWARE MONITOR*, LADDER MONITOR*] DATA ERASE window ACCUMULATED TIME window Description of displays marked with an asterisk (*) is omitted because these displays are reserved for YAMAZAKI MAZAK servicemen. 10-1 DIAGNOSIS (USER) – ALARM Display Function: - Displaying the number, details, etc. of alarms currently occuring...
- Page 315 Return to Library 10-1-1 Data display Displayed data  #  $  %  &  ' D735S1065E Display data description Item Unit Data description Alarm number • • Alarm contents ALARM MESSAGE • • Section where the alarm occurred ( a, b, c ) a: Work number •...
- Page 316 Return to Library DATA ERASE window This window is used to erase the entire data of, or to initialize, the particular display. Press the DATA ERASE menu key. Î The display of the menu item will be reversed and the DATA ERASE window will appear. Select the display(s) to be initialized.
- Page 317 Return to Library Using the cursor key, move the cursor to the line of the desired item. Example: If the cumulative time of automatic cutting is to be set Specify the time, and press the INPUT key. Example: To set 11: 05’ 38’’, press keys in the following order: •...
- Page 318 Return to Library 10-2 DIAGNOSIS (USER) – ALARM HISTORY Display Function: Displaying the details, the places of occurrence, etc. of all alarms that have occurred up to now, in order of the latest alarm first. 10-2-1 Data display Displayed data Â...
- Page 319 Return to Library 10-3 DIAGNOSIS (USER) – PLC SIGNAL Display Function: Displaying ON/OFF status of machine signals 10-1-1 Data display Displayed data  #  $  #  $  #  $  #  $ D735S1067E Display data description Item Unit Data description...
- Page 320 Return to Library 10-4 MAINTENANCE CHECK Display Function: - Periodic check items, the last date of checking, and the time that has elapsed since the last date of checking are displayed. - Periodic check items can be registered. Remarks: The machine will not stop even if the display of the time which has elapsed since the last date of checking exceeds the target time.
- Page 321 Return to Library Registering the data for regular check items Presetting the target time or the current time Move the cursor to the data item where data is to be preset. Enter time. Example: Specify “96” and press the INPUT key to input 96. Note: Entry of the current time updates the data of data item •...
- Page 322 Return to Library 10-1-4 Entry of the check items to be displayed The check items to be displayed cannot be entered directly on the MAINTENANCE CHECK display. This subsection describes the procedure for adding or deleting the check items to be displayed.
- Page 323 Return to Library characters). Excess items or characters will be ignored. Read and Write of check items’ text file All the check items presented on the MAINTENANCE CHECK display can be read in from, and written into, the specified text file. Use a commercially available editor to prepare a text file containing the desired check items to be read in and presented on the display.
- Page 324 Return to Library 10-5 PLC Display Function: Displaying informations provided for the individual machine. 10-5-1 Data display Displayed data D735S1070E Note: The data on this display differs from machine to machine. Refer to the Manuals for the machine. 10-11...
- Page 325 Return to Library 10-6 RUNNING CONTROL Display Function: Displaying the machine operational status. Remarks: - The machine operational status for the last seven days (one week) is displayed. - The operational status during power-on time is displayed in distinction between the following four divisions: Running in automatic operation Stopping in automatic operation...
- Page 326 Return to Library Displayed data with reverse display of RUNNING COND. menu item  #  $  %  & D735S1072E 10-13...
- Page 327 Return to Library Displayed data with reverse display of SPINDLE LOAD menu item  #  $  '  ( D735S1073E Display data description Item Unit Data description - Date and cumulative power-on time for the operational status display a ( b ) •...
- Page 328 Return to Library Item Unit Data description - Graphic display of change in spindle speed. –1 • MAX.ROT. - The change in spindle speed during power-on is displayed in a red line. - Graphic display of change in spindle load. •...
- Page 329 Return to Library Changing from the total to the display mode for each work number Call up the cursor in the column of DATE/TIME by pressing a cursor key. - The cursor here refers to a rectangular section displayed in reverse, as shown below, in the DATE/TIME column.
- Page 330 Return to Library - Pressing the RUNNING COND. menu key anew will clear the reverse display of the menu item to retrieve the total display mode. Changing from the total to the display mode for spindle load Call up the cursor in the column of DATE/TIME by pressing a cursor key. - The cursor must be called up first, as is the case with the change to the display mode for each work number.
- Page 331 Return to Library 10-7 DIAGNOSIS (MAKER) – VERSION Display Function: Displaying versions of NC unit and servo axes 10-1-1 Data display Displayed data  )  %  &  #  $  #  $  '  ( Â...
- Page 332 Function: - Display of memory status in the NC unit - You can write data into the memory. Remarks: Please follow the instructions of YAMAZAKI MAZAK servicemen when writing data into the memory. 10-1-1 Data display Displayed data  # Â...
- Page 333 Return to Library Item Unit Data description Address when writing data into I/O address ADRSS • • Data Data display in binary for the address in item • • • Data Data display in hexadecimal for the address in item • •...
- Page 334 MEMORY MONITOR WRITE ADDRESS 76543210 NW00123456 00011010 Note: Please follow the instructions of YAMAZAKI MAZAK servicemen when writing data into the memory. Writing data in hexadecimal into the I/O memory Place the cursor on the ADRSS item of I/O MONITOR WRITE. Example:...
- Page 335 00F1 Note: Write data in accordance with the directions of a YAMAZAKI MAZAK serviceman. Writing data in decimal form into the I/O memory Carry out the same operations as those of steps (1) and (2) which are to be taken when writing data in hexadecimal form into the I/O memory.
- Page 336 Return to Library 10-9 DIAGNOSIS (MAKER) – OPTION Display Function: Displaying all optional functions for the NC unit Remarks: All terms are displayed in English on this display. 10-9-1 Data display Displayed data  #  #  # D735S1076E Display data description Item Unit...
- Page 337 Return to Library - NOTE - 10-24...
- Page 338 Return to Library 11 OPTION 11-1 Machining Management Functions 11-1-1 General The machining management functions are designed so that machining management information for each pallet can be managed by saving the information into a PALLET MANAGEMENT display area and pallet ID information separate from the machining program data field. This allows the machining program sequence to be changed according to the status of the workpiece without updating the program.
- Page 339 Return to Library 11-1-2 PALLET MANAGEMENT display Displayed data  (  )  *  #  $  %  &  '  +  , D735S1077E Displayed data for each function is described below. 11-2...
- Page 340 Return to Library 11-1-3 Scheduled-operation function Data of the PALLET MANAGEMENT display Data displayed for the scheduled-operation function (• through •) is described below. Display data description (1/4) Data name Description PALLET Number of pallets that is initially set for the particular machine specifications. •...
- Page 341 Return to Library Setting data in the STATE item Set the status of machining on each pallet. Move the cursor to the STATE item using the cursor key. PALLET WNo. STATE ORDER NUMBER • Move the cursor to this position. Μ...
- Page 342 Return to Library Changing data in ORDER When changing the machining order that has already been set, move the cursor to the ORDER item, enter new data using the appropriate numeric key(s) and press the INPUT key. The ORDER item data for other pallets are auto-changed. Example: Updating the data of ORDER in line PALLET 4 to “1”.
- Page 343 Return to Library (2) Press the PLURAL PROCESS menu key. (3) Press the INPUT key. Î For the PALLET No. specified in procedure (1), multiple processes are set. PALLET WNo. STATE ORDER READY READY READY • READY READY READY READY Μ...
- Page 344 Return to Library ALL ERASE This function clears the entire schedule that has been set (A to E). <Setting method> Press the ALL ERASE menu key. When the message ALL ERASE <−9999 INPUT>? is displayed, enter “−9999” and then press the INPUT key. The display will then be initialized.
- Page 345 Return to Library Precautions Editing in the scheduled-operation mode - Even during scheduled operation, editing can be done on the PALLET MANAGEMENT display, except for the line of 1 under ORDER item (machining now in progress). See “2. Data editing methods”, for further details of editing. - If the machining for the pallet of CUTTING is finished during EDIT mode, the machine will be stopped.
- Page 346 Return to Library 11-1-4 External unit skipping function Data of the PALLET MANAGEMENT display. Display data description (2/4) Data name Description The pallet number corresponding to data • is displayed. PALLET No. • The work number corresponding to data • is displayed. WNo.
- Page 347 Return to Library Operation A specific example is shown below. Example: Pallet 1 Pallet 2 WNo. WNo. WNo. WNo. Unmachined Unmachined Machined M3S045 Program WNo. 1 (Main program) θ UNo. UNIT WPC-1 –300 –300 –400 UNo. UNIT WORK.No. REPEAT SUB PRO UNo.
- Page 348 Return to Library 11-1-5 External multi-piece machining function Data of the PALLET MANAGEMENT display. Display data description (3/4) Data name Description Multi-piece machining will be performed if the bits corresponding to the multi-piece MULTIPLE SWITCH • machining flag (MULTI FLAG) on the program are correspondingly set. Entering data Set MULTIPLE SWITCH as follows to activate the external multi-piece machining function.
- Page 349 Return to Library Program WNo. 1 (Main program) UNo. INITIAL-Z ATC MODE MULTI MODE MULTI FLAG PITCH-X PITCH-Y 5 ∗ 2 CST IRN 1100010101 θ UNo. WPC-1 -300 -300 -400 UNo. LINE OUT• SNo. E-MILL• SQR• UNo. UNIT WORK No. REPEAT SYB PRI UNo.
- Page 350 Return to Library The machining is executed according to the common data which is included both in MAIN and MULTI FLAG of the main program, or both in A to D (set in $ of the subprogram unit) and MULTI FLAG of the subprogram.
- Page 351 Return to Library Meaning of jig offset data When, as shown below, the reference point differs between the reference pallet jig (indicated by a discontinuous line) and the intended jig (indicated by a continuous line), set the amounts of offset at a table angle of 0 degrees (∆x, ∆y, ∆z) as the offsetting data for the jig you are going to use.
- Page 352 Return to Library Since the jig offsetting function only corrects any offsets in each axis direction, no corrections are performed for any offsets in the rotational direction of each axis. 1) X-Z direction Offsetting possible Offsetting impossible M3S049 2) Y direction Offsetting possible Offsetting impossible M3S050...
- Page 353 Return to Library 11-1-7 Parameters The following lists parameters related to the machining management functions: Parameter Setting value Description The machining management functions become invalid. Valideated for operation of MAZATROL-FMS with pallet ID-function. Machining management operation for multiple-pallet system is selected. On the PALLET MANAGEMENT display, work numbers are: Displayed Not displayed...
- Page 354 Return to Library Making an updating program Make an updating program into a configuration that allows a macro-program to be called using a subprogram unit of a MAZATROL program. MAZATROL program to be used for call A calling program must be made as follows. Otherwise, the machine will operate incorrectly. Calling program Macroprogram Machining unit...
- Page 355 Return to Library (5) When using an argument(s), move the cursor to the ARGM item and set an argument(s) using the numeric keys. UNo. UNIT WORK No. SUB PRO 1234 • SNo. ARGM1 <Supplementary description> The following lists restrictions, and the reasons, as to the making of a calling program: Restriction 1 The write macro calling subprogram unit must end with an end-of-process unit.
- Page 356 Return to Library setting data for these variables. To let the NC perform write operations, system variables for write control must be further set. Write control system variables are listed in the table below. <Write control system variables> Data name System variables number Setting Write data valid flag...
- Page 357 Return to Library To write data as shown above, make a macro-program for updating the machining management data as follows: Main program Macro program #50467 = 0 #50443 = 307 #50467 = #50467 OR 1 #50441 = 15 #50467 = #50467 OR 2 #50435 = 224 End-of-process unit #50467 = #50467 OR 4...
- Page 358 Return to Library 11-2 Function Relating EIA/ISO Program (Option) EIA/ISO ONLY menu item will be displayed on the DIAGNOSIS (ALARM) if an EIA/ISO programming option is added. Pressing the menu key will reverse the display status of the menu item and modify the display configuration and various data items into ones that can be more conveniently used for EIA/ISO program.
- Page 359 Return to Library Configuration of displays - when EIA/ISO ONLY is reversed - PART SHAPE WORK No. MONITOR POSITION HANDLE COMPARISON RESTART INTERRUPT STOP∗ MONITOR TRACE WORK OFFSET MEASURE PALLET MACRO ∗ MANAGEMENT VARIABLE ∗ WORK No. WORK No. POSITION PROGRAM MONITOR POSITION...
- Page 360 Return to Library WORK No. DATA SPINDLE LOAD MACHINING MACHINING- GRAPHIC NAVIGATION- MONITORING DISPLAY RESULT Main display Sub-display Window ∗ Optional The displays connected by the line can be called up mutually by pressing menu key. ∗1 Only for machines with multiple-surface machining function ∗2...
- Page 361 Return to Library 11-2-2 POSITION display POSITION display is changed as follows when the EIA/ISO ONLY menu item is reversed. Displayed data when the COMMAND menu item is not reversed D735S1079E 11-24...
- Page 362 Return to Library Displayed data when the COMMAND menu item is reversed D735S1080E Display data description Item Unit Data description Work number of the program being executed (a' b') • • Work numbers a’ Identification of MAZATROL or EIA/ISO program b’...
- Page 363 Return to Library 11-3 Workpiece Measurement Printout System 11-3-1 Function overview The workpiece measurement printout system has been developed to take automatic measurements of hole and boss diameter, groove and step width, center to center distance, step differences and other distances between randomly selected points, angles of slant and the like, and to provide printouts of the results of these measurements.
- Page 364 Return to Library Measurement function Random workpiece lengths or angles are measured by the touch sensor tool. A wide variety of measurement patterns are available for selection. Patterns available are described in the following charts. Measurement group Measurement patterns Diameter/width measure- ment: Designate center coordinate ID and OD...
- Page 365 Return to Library Examples of measurement between two randomly selected points: X-surfcace to X-xurface (step) Step center X to X-surface Groove center X to groove center X Hole center to holde center (distance between centers) Hole center to outside corner Outside corner to outside corner M3S073 - The number of machining cycles to be conducted between measurements is designated by a...
- Page 366 Return to Library Tolerance judgment function Upper tolerance limit(u) u – v u – v q × Target value u – v q × u – v Lower tolerance limit (v ) M3S074 Tolerance judgment is classified in three stages according to the upper tolerance limit (u), the lower tolerance limit (v) and the compensation range setting rate (q).
- Page 367 Return to Library Compensation function TOOL DATA display Tool diameter Tool length TOOL OFFSET (TYPE A) display Offset data Designation of the tool number or the offset number of the end mill that was used on the measured surface allows compensation to be made in the relevant tool diameter, tool length and offset data. Compensation for OFFSET DATA can not be made when setting TOOL OFFSET in type B.
- Page 368 Return to Library Printout function The printout function can be controlled in any of three different ways, depending on parameter settings. These are indicated below: Printout not required This selection is made when the system is to be operated with the measurement, tolerance judgment and compensation functions only, or when printer failure or some other reason makes it impossible to use the printer.
- Page 369 The workpiece measurement printout function is composed of the following components: a touch sensor tool that is brought into contact with the measurement surface; a MAZAK measuring system (MMS) receiver that receives contact signals from the touch sensor; the MAZATROL NC unit, which reads coordinate values when contact is made between the touch sensor and the measurement surface;...
- Page 370 Return to Library Printer Printer for this system The printer used in this system is an Epson P-40 printer, which is interfaced with the NC unit using PTP/PTR connector. NM210-00449 Part name Part name Printer cover Power connector Paper cutter Interface connector PF switch DIP switches...
- Page 371 Return to Library 11-1-3 Parameter registration Before attempting to utilize the workpiece measurement printout function, it is necessary to first register in the common variables the parameter settings which designate the data management system to be used and the compensation amount of touch sensor tool. For data management system parameters, refer to 2.
- Page 372 Return to Library Data management system parameters Item Address Value to register Mesurement cycle #500 Register number of cycles in which measurement is to be made. If #500 is set at “0”, no measurement will be made at all. Printout categories #501 0.
- Page 373 Return to Library Touch sensor tool compensation amount ÄC Sytlus ball contact circle center “A” View Tool shank center M3S078 Eccentricity compensation values “ex” and “ey” and measurement compensation values “Mx” and “My” must be registered as common variables before any attempt is made to use the touch sensor to measure a workpiece.
- Page 374 Return to Library 11-1-4 Program configuration The workpiece measurement printout function is used by adding a macroprogram call command to the main program. Before this program is called out, however, it is necessary to designate the workpiece coordinate system. Tool exchange commands for the touch sensor are executed by the workpiece measurement initial setting program, and they do not have to be added to the main program.
- Page 375 Return to Library Macro program The workpiece measurement printout system is made up of the 15 macroprograms indicated in the following table. The program necessary for the measurement pattern to be executed should be selected. Group Work No. Type of measurement Argument address Initial setting 9100...
- Page 376 Return to Library A total of 10 different combinations is possible for workpiece numbers 9120 through 9123, depending on the designation of arguments at measurement points 1 and 2. Compensation Program combination Measurement pattern Direction setting (Note 1) 9120 - 9120 Surface to surface X, Y, Z •...
- Page 377 Return to Library Multiple group measurements - It is possible to designate measurements to be made from each group (A, B, and C) within the same main program. In such cases, the workpiece measurement initial setting program is necessary only once, at the beginning. 9100 9100 9100...
- Page 378 Return to Library Examples for calling up a macroprogram EIA/ISO programs Workpiece offset X -360. G54 Coordinate system setting Y –450. Z -600. Workpiece measurement initial setting G65P9100W1200.R5.K3.Q0.5 Measurement (example is ID) G65P9110M101.X200.Y200.Z-5.D100. G65P9115U0.1V-0.1S2. Tolerance judgment, printout Note: G90/G91 and F-code modal information is updated according to workpiece measurement. MAZATROL program language program UNo.
- Page 379 Return to Library 11-1-5 Explanations of macro programs Workpiece measurement initial setting (WNo. 9100) This program is responsible for the designation of common data to be used in workpiece measurement, the initializing of common variables, workpiece counting management and the automatic tool change operation for the touch sensor.
- Page 380 Return to Library This data is not effective during slant measurement. #554 (nominal radius of probe) X, Y directions Z direction M3S079 When performing slant measurement, set the measurement start point in such a way that it will be within 15 mm (0.6 inch) of the measurement point. Qq: Compensation field setting rate (0 to 1.0) Set ratio of the range that will not result in compensation conducted, with respect to tolerance width 1.0.
- Page 381 Return to Library [Measurement operations] m = 1. ID Measurement m = 2. OD measurement Workpiece zero point Workpiece zero point M3S082 M3S083 m = 3. ID Measurement II Workpiece zero point - Measurement pattern is determined in accordance with the value of argument “m” as shown in the accompanying diagrams.
- Page 382 Return to Library Groove width and step width measurements (WNo. 9111) Groove and step width are calculated by measuring both ends of the groove or step section (along either the X-axis or the Y-axis direction) EIA/ISO P9111 UNo. UNIT WORK No. REPEAT SUBPRO 9111E...
- Page 383 Return to Library [Measurement operations] m = 1. X-axis groove width measurement m = 2. Y-axis groove width measurement M3S085 M3S085 m = 3. X-axis step width measurement m = 4. Y-axis step width measurement M3S085 M3S085 - Values of “r” and “k” are designated in the workpiece measurement initial setting program (WNo. 9100).
- Page 384 Return to Library Tolerance judgment printout A (WNo. 9115) This program compares the results of the measurements of inner diameters, outer diameters, groove widths and step widths with the target values; makes a tolerance judgment on the basis of this comparison, and prints out the results of this judgment. Tool diameter compensation can also be made, depending on the amount of error in measured values in respect to the target values.
- Page 385 Return to Library Surface measurement (WNo. 9120) This program allows measurement of a surface workpiece coordinate. It is combined with other measurement patterns to calculate distance to the surface. EIA/ISO P9120 UNo. UNIT WORK No. REPEAT SUBPRO 9120E MAZATROL SNo. ARGM 1 ARGM 2 ARGM 3...
- Page 386 Return to Library [Measurement patterns (“m ” corresponds to the ones integer of argument m)] = 4. = 5. –Y = 1. = 2. –Z –X = 3. M3S087 [Measurement operations] X, Y surface (in the case of +X) Z surface Workpiece Workpiece zero-point...
- Page 387 Return to Library Groove center and step center measurement (WNo. 9121) Ths program measures both edges of grooves and step sections (in the X-axis or Y-axis direction) and calculates the center coordinates of the groove or step section from these measurements. It is combined with other measurement patterns to calculate the distance to the groove or step section center.
- Page 388 Return to Library - Measurement operations (“m ” corresponds to the ones integer in argument “m”) = 1. X-axis groove center measurement = 2. Y-axis groove center measurement M3S089 M3S089 = 3. X-axis step section center measurement = 4. Y-axis step section center measurement M3S090 M3S090 - Values of “r”...
- Page 389 Return to Library Hole center and boss center measurement (WNo. 9122) This program calculates center coordinates (X and Y) by the measurement of four points on a circle. Measurement is made first along the X-axis, then along the Y-axis. It is combined with other measurement patterns to calculate the distance to a hole or boss center.
- Page 390 Return to Library - Measurement operations (“m ” corresponds to the ones integer in argument “m”) = 1. Hole center measurement = 2. Boss center measurement Workpiece zero point Workpiece zero point M3S082 M3S083 = 3. Hole center measurement II Workpiece zero point - Measurement pattern is determined in accordance with the value of argument “m...
- Page 391 Return to Library Outside and inside corner measurement (WNo. 9123) This program performs continuous measurement of an X surface and a Y surface to calculate the corner coordinate value (X and Y). It is used in combination with other measurement patterns to calculate the distance to the corner.
- Page 392 Return to Library [Measurement patterns] (“m ” corresponds to the ones integer of argument m) Inside Corner Outside Corner = 4. = 3. = 8. = 7. = 1. = 2. = 5. = 6. M3S091 [Measurement operations] Outside Corner Inside Corner (in the case of m = 1.)
- Page 393 Return to Library Tolerance judgment printout B (WNo. 9125) This program compares the distances between measurement point 1 and measurement point 2 as measured in combination with coordinate value measurements (WNo. 9120 through 9123) with the target values; makes a tolerance judgment on the basis of this comparison, and prints out the results of this judgment.
- Page 394 Return to Library - Compensation operation b = 1. Inner compensation as seen from reference point b = –1. Outer compensation as seen from reference point Diameter compensation tool Diameter compensation tool X or Y Measured distance Measured distance Coordinate Reference value to be coordinate...
- Page 395 Return to Library Slant measurement and tolerance judgment printout C (WNo. 9130/9135) This program measures two points on the workpiece surface and calculates the angle of slant in respect to the coordinate axis; compares the results to a target value to make a tolerance judgment, and prints out the result of this judgment.
- Page 396 Return to Library - The coordinate value of measurement starting point 2 is automatically determined according to the measurement starting point, the axis movement amount and the target angle. It is therefore especially important to take care about signs of axis movement amount “i” and target angle “a”. a (+) a (–) a (–)
- Page 397 Return to Library [Measurement operations] When f = 1. and m = 3. When f = 2. and m = 5. Workpiece Workpiece zero-point zero-point (i > 0) (a > 0) (i > 0) (a < 0) M3S099 M3S098 - The measurement start point should be set within 15 mm (0.6 in.) of the measurement point. Measurement point Measurement point Start point...
- Page 398 Return to Library [Defining the measured angle] f = 1.; X-Y surface Measurement direction a > 0 a < 0 m = 1. m = 2. –X m = 3. m = 4. –Y M3S102 “P1” is the measurement start point designated by arguments “x” “y” and “z”. “P2” is determined automatically according to the values of arguments “i”...
- Page 399 Return to Library f = 2.; X-Z surface Measurement direction a > 0 a < 0 m = 1. m = 2. –X m = 5. –Z M3S103 “P2” is determined automatically according to the values of arguments “i” and “a”. In the above example, i >...
- Page 400 Return to Library f = 3.; Y-Z surface Measurement direction a > 0 a < 0 m = 3. m = 4. –Y m = 5. –Z M3S103 “P1” is the measurement start point designated by arguments “x” “y” and “z”. “P2”...
- Page 401 Return to Library 11-1-6 Program and measurement pattern chart Group Work No. Measurement patterns (m 9110 ID II M3S104 9111 X groove width Y groove width X step width Y step width M3S105 4. –Y 5. –Z 1. +X 2. –X 9120 M3S106 3.
- Page 402 Return to Library 11-1-7 Output of measurement results Contents of printout The contents of the printout are automatically controlled by the type of data processing system being used. A maximum of 8 items can be included in one print cycle. Format (Differs by contents of the printout) Millimeter: Integer: up to four figures;...
- Page 403 Return to Library Measured values The actually measured lengths and angles are also printed with the comments according to the format shown below. Length Angle Comment Length on X-axis Angle with X-axis MEASURED DATA X Length on Y-axis Angle with Y-axis MEASURED DATA Y Length on Z-axis Angle with Z-axis...
- Page 404 Return to Library - Items printed •: Printout ×: Not printout Componsation indicated/ not indicated Tolerance not Compensation Item indicated Judgment results outside made compensation Workpiece No. and workpiece count • • • Target value • • • Measured value •...
- Page 405 Return to Library 11-1-8 Alarm displays An NC alarm will be generated in the event that a programming error or a malfunction in the touch sensor prevents an accurate measurement from being made or in case of tolerance over state. An alarm message will be displayed on the CRT screen if an alarm is generated.
- Page 406 Return to Library 11-1-9 Program and printout example The following example illustrates tool diameter compensation made for Tool No. 20 as the result of ID measurement. Program (EIA/ISO) Μ G65P9100W1234.R10.K3.Q0.5 G65P9110M101.X-50.Y-50.Z-5.D50. G55P9115U0.3V0.S20. Μ Print out /RESULT OF MEASURING/ 1234 COUNT 1 φ50.
- Page 407 Return to Library The following example illustrates compensation made for Offset No. 30 as the result of measurements of hole center as reference and surface. Program (EIAISO) Μ G65P9100W5678.R10.K4.Q0.5 100. (P1) G65P9122M11.X-100.Y-60.Z-20.D60. 60 ± 0.1 (P2) G65P9120M122.X-40.Y-60.Z-20. G65P9125E1.U0.1V-0.1S30.B-1. Μ (∗) Printout φ60.
- Page 408 Return to Library The following example illustrates a measurement made between two outside corner points and a tolerance judgment made along the X-axis and the Y-axis. Program (EIA/ISO) Μ G65P9100W2468.R15.K5.Q0.5 (P1) G65P9123M14.X-80.Y0.Z-10.I15. (P2) G65P9123M122.X0.Y-60.Z-10.I15. 80 ± 0.1 G65P9125E1.U0.1 V-0.1 G65P9125E2.U0.05 V–0.05 Μ...
- Page 409 Return to Library Continuous measuring of X-axis distance between hole center and groove center, and Y-axis distance between hole center and plane. Program (EIA/ISO) Μ G65P9100W3690.R20.K3.Q0.5 (P1) G65P9122M11.X-48.Y-60.Z-15.D60. (P2) G65P9121M121.X-120.Y-60.Z-15.D32. 120. G65P9125E1.U0.05 V–0.05 72 ± 0.05 P2’ (P2’) G65P9120M124.X–120.Y0.Z-15. G65P9125E2.U0.1V–0.1 Μ...
- Page 410 Return to Library Measuring slant angle between two planes on X-Y plane Tolerance: ±0.2 deg. Program (EIA/ISO) Μ G65P9100W1496.R10.K5.Q0.5 G65P9130F1.M3.X–420.Y–200.Z–20. G65P9135I200.A–30.U0.2V–0.2 G65P9130F1.M102.X–130.Y–270.Z–20. G65P9135I110.A30.U0.2V–0.2 Μ 420. 130. Print out 110. 200. /RESULT OF MEASURING/ 270. 1496 COUNT 1 30° MARK DATA SLANT X-Y –30.000 30°...
- Page 411 Return to Library 11-4 Geometry Compensation Function 11-4-1 Function general Machining at rapid feed will generally degrade a geometry accuracy in proportion to the feed rate. For example, delayed follow-up of smoothing circuit and servo system occurs in circular cutting, making a smaller workpiece than commanded circle radius.
- Page 412 Return to Library Active feedforward control Pre-interpolation accelerate/ decelerate commands Active feedforward control Post-interpolation accelerate/decelerate commands – – Detector Kp: Position loop gain Kv: Velocity loop gain Motor Differential Note: Active feedforward control is valid only when the geometry compensation function is valid.
- Page 413 Return to Library 11-4-2 Detailed description Programming format MAZATROL program For MAZATROL programs the geometry compensation function becomes automatically valid through the setting of user-parameter F72. F72 = 1: Geometry compensation function valid User-parameter F72 = 0: Geometry compensation function invalid It is also possible to validate/invalidate the geometry compensation function by setting M153/M154 under M-code article either of tool sequence data in a machining unit or of a manual program mode unit.
- Page 414 Return to Library EIA/ISO Program G61.1 Geometry compensation function valid (Exact stop check mode) Geometry compensation function invalid (Automatic corner override) (Command codes of the same group cancel the mode.) (Tapping mode) (Cutting mode) Note: In the case of EIA/ISO programs, it is always necessary to give the G-code command to make the geometry compensation function valid since the setting of parameter F72 is not effective for them.
- Page 415 Return to Library The acceleration/deceleration pattern is shown below. Velocity Gradient-fixed acceleration/deceleration Programmed velocity Time Gradient-fixed execution time Optimum corner deceleration Machining with high edge precision can be done by decelerating the machine at corners. Before it arrives at corner point P, the machine is automatically decelerated to achieve its maximum permissible deceleration value, Vo.
- Page 416 Return to Library If the intersection angle, θ, of the path of the current block and that of the next one is the value of parameter L77 or less, these two paths will be judged smooth and no deceleration will occur. If this angle is in excess of the value of parameter L77 the paths will be judged nonsmooth and optimum corner deceleration will be performed.
- Page 417 Return to Library As shown on the left, the programmed path may not be smooth, Programmed path If this is the case, the velocity will be reduced and optimum corner deceleration will occur. Rough interpolation Programmed path Reduction of the velocity moves the tool almost as programmed, thus allowing precise Precise vector interpolation...
- Page 418 Return to Library Accuracy coefficient Under corner- and arc-machining commands, optimal corner deceleration and arc feed rate limitation provide automatic deceleration to compensate for any errors in the accuracy of machining. In that case, machining accuracy can be further improved by specifying an accuracy coefficient in the program since further deceleration is achieved at corners and at arc sections.
- Page 419 Return to Library 11-1-4 Notes This feature works only under optional specifications for geometry compensation function. A program error (Alarm 935 NO PRE-INTERP ACCEL/DECEL OPT.) will result if programming is done using this feature under the standard specifications for usual machining. Pre-interpolation acceleration/deceleration is valid for the G61.1 command block onward.
- Page 420 Return to Library 11-1-6 Appendix Appended data concerns theoretical values obtained from the conditions of commanded radius, feedforward gain, etc. They may differ from measured values in actual machining depending on cutting conditions, machine accuracy, etc. Apply it as a general criterion for test cuts and others. Maximum feed rate in circular interpolation when geometry compensation function is valid Maximum feed rate in circular interpolation when geometry compensation is valid can be determined from the following equation.
- Page 421 Return to Library When geometry compensation function is invalid (In exponential acceleration/deceleration system) ∆ R × R F × 10 × 60......• F : Maximum feed rate (m/min) Tp : Position loop time constant (sec) (= 1/SV003) Kf : Feedforward gain ( = S5/100) ∆R : Geometry error (mm) R : Circle radius (mm) Each maximum feed rate within 10 µ...
- Page 422 Return to Library 30000 (mm/min) (msec) Feedforward gain 0.85 Geometry error 0.01 (mm) Time constant (G61.1) (sec) Position loop time constant 0.03 (sec) Time constant (G64) 0.02 (sec) Geometry compensation function valid Normal cutting mode R (mm) Maximum feed 1 Error Maximum feed 2 Error...
- Page 423 Return to Library 11-5 Hard Disk Operating Function 11-5-1 Outline With the hard disk (HD) operating function, any large-size EIA/ISO program presaved within a special folder of the HD contained in the NC unit can be executed for automatic operation while transferring that program to the NC memory.
- Page 424 Return to Library HD operation modes The HD operating function can be used in the following two modes: Direct operation mode A program stored on the HD operates as the main program. Subprogram operation mode A program stored on the HD is called up as the subprogram from a main program registered in the NC memory.
- Page 425 Return to Library an HD program. The HD subprogram is always executed from the beginning. - Repeat time specification for subprogram call is not effective in calling up an HD program. The HD subprogram is always executed only one time for one call command. - The subprogram call from the NC main program preferably selects a program in the NC memory to that on the HD in case the specified work number should have been assigned to the both programs.
- Page 426 Return to Library Subprogram operation mode Select the machine operating mode for the subprogram operation mode. - Press the MEMORY operation key Select the POSITION display on the screen. - This is required for selecting the program to be run and checking the operational status of the machine.
- Page 427 Return to Library Programming format Create HD operation programs in the following text file format: - One program must be created for one text file. - The program must not begin with an EOR code (%) since it is executed from the very first block. - Enter a line feed code (by pressing the return key) at the end of each block.
- Page 428 Return to Library 11-1-7 Alarms concerned Type of Stopped Clearing Message Display error status procedure PROGRAM No. NOT FOUND Blue An attempt has been made to select a program with the work number not regitered on the HD or in the NC memory. Cause Check and select the correct work number.
- Page 429 Return to Library 11-6 IC Memory Card Operating Function 11-6-1 Outline With the IC Memory Card (abbreviated to CARD in this section) operating function, any large-size EIA/ISO program presaved within a special folder of the CARD set into the slot on the front of the NC operating panel can be executed for automatic operation while transferring that program to the NC memory.
- Page 430 Return to Library CARD operation modes The CARD operating function can be used in the following two modes: Direct operation mode A program stored on the CARD operates as the main program. Subprogram operation mode A program stored on the CARD is called up as the subprogram from a main program registered in the NC memory.
- Page 431 Return to Library For subprogram operation mode - The CARD subprogram cannot call another CARD program as a subprogram. On a further sub- program-call command from the CARD subprogram can only the NC memory be searched for, and an alarm will be given if the specified program is not found there. - Sequence number specification for subprogram call by “...
- Page 432 Return to Library Subprogram operation mode Select the machine operating mode for the subprogram operation mode. - Press the MEMORY operation key Select the POSITION display on the screen. - This is required for selecting the program to be run and checking the operational status of the machine.
- Page 433 Return to Library Programming format Create CARD operation programs in the following text file format: - One program must be created for one text file. - The program must not begin with an EOR code (%) since it is executed from the very first block. - Enter a line feed code (by pressing the return key) at the end of each block.
- Page 434 Return to Library 11-1-7 Alarms concerned Type of Stopped Clearing Message Display error status procedure PROGRAM No. NOT FOUND Blue An attempt has been made to select a program with the work number not regitered on the CARD or in the NC memory. Cause Check and select the correct work number.
- Page 435 - Boring (Roughness level 2 to 9) - Chamfering (Cycle 2) - End-milling (Cycles 2, 3) Output with a code from G0 to G4 - Tornado cycle Point- - MAZAK precision high-speed machining tornado boring - Planet tapping Synchronous tapping Output with G84/G74 or G84.2/G84.3 (Parameter-selectable)
- Page 436 Return to Library 11-7-2 EIA conversion program format The format of program conversion from MAZATROL into EIA is shown below. The work number of the source program is assigned on the first line and comments are automatically inserted for each tool sequence.
- Page 437 Return to Library 11-1-4 Operating procedure Move the cursor on the PROGRAM FILE display to the line where the work number of the program to be converted is displayed. - The cursor can be set at any of the items present on the line where the work number of the intended MAZATROL program is displayed.
- Page 438 Return to Library Parameter F97 can be used to select the type of coordinate system to be used for an EIA/ISO converted program. Coordinate system (Codes A to J or codes G54.1P1 to G54.1P48 cannot be selected) To select external WPC using the WPC unit of the conversion source program, set any command code from G54 to G59.
- Page 439 Return to Library (a) X- and Y-axis line machining, groove machining, and face machining (F-MILL (bidirectional cut), TOP EMIL) are set as a subprogram. Example: Approach Escape path path X- and Y-axial machining are set as a Z-axial cutting is set as the mainprogram. subprogram.
- Page 440 Return to Library (b) Face machining is set as a subprogram (F-MILL (unidirectional), STEP, POCKET, PCKT MT, PCKT VLY) Example: Main program Subprogram Rapid feed Cutting feed Main program WNo. 2001 Subprogram WNo. 2002 N10(2000-1-1) (P2000) G17G00G40G54G64G90G94G98 G0Z Initial point N10(2000-1-1) G1Z# Variable number G1Z Cutting face height (1)
- Page 441 Return to Library For EIA conversion 2, since the point-machining unit is converted into a standard fixed-cycle code, the machine does not operate as minutely as with the original MAZATROL program. Operational characteristics in that case are listed below. - Cutting clearances always become equal to the setting of parameter D41. - Deceleration for escape is not valid for drilling.
- Page 442 Return to Library 11-1-6 Parameter and alarm lists Parameters relating to EIA/ISO conversion are listed below. Parameter list Parameter Function Setting Description 0: Subprogram creation invalid F88 bit 0 Subprogram creation 1: Subprogram creation valid 0: Fixed-cycle G-code output (EIA conversion 2) F88 bit 2 Point-machining G0-G4 output 1: G0-G4 code output (EIA conversion 1)
- Page 443 Return to Library Return to Library...
- Page 444 Return to Library...
- Page 445 Return to Library Fusion 640M Auto Operation SAFETY PRECAUTIONS ..............Lockout Procedure .................... Installation Precautions ..................Warnings ......................1 AUTOMATIC OPERATION EXECUTION ......... 1-1 Automatic Operation Execution Procedure ..........1-2 Types of Automatic Operation Mode ............1-2-1 Automatic operation ....................1-2-2 Restart operation ......................
- Page 446 Return to Library 2-7-2 Description ......................... 2-8 Z-axis Cancel ....................2-8-1 Procedure ........................2-8-2 Description ......................... 2-9 MST Lock ....................2-9-1 Procedure ........................2-9-2 Description ......................... 2-10 ATC Stop ....................2-11 TUNING SV PARAM ................. 2-11-1 Operation procedure ....................2-11-2 Function description ....................
- Page 447 Return to Library 4-5 Single-block Stop ..................4-5-1 Single-block stop by changing within automatic operation modes ......4-5-2 Single-block stop using the SINGLE BLOCK key ............4-6 Program Stop ....................4-7 Stopping by Turning the Power Off ............. 5 MANUAL INTERRUPTION ...............
- Page 448 Return to Library...
- Page 449 Return to Library AUTOMATIC OPERATION EXECUTION Automatic operation of the machine according to previously created programs and data is referred to as automatic operation. Automatic operation becomes possible just by selecting the program to be executed and then starting it, provided that errors are not present in the program or data. No other operations are required.
- Page 450 Return to Library Calling up the program to be executed in the automatic operation mode Selecting automatic operation execution conditions - Single-block and optional-stop operation - Dry run and machine locking - Coolant injection Adjusting the cutting conditions - Rapid feedrate overriding - Cutting feedrate overriding - Spindle speed overriding Mounting a workpiece...
- Page 451 Return to Library Types of Automatic Operation Mode Automatic operation can be executed using the programs registered within the NC unit or EIA/ISO programs stored on paper tapes, microdisks, or other such external media. The machine can also be made to automatically execute non-program data that the operator may have set as required.
- Page 452 Return to Library 1-2-1 Automatic operation Memory operation mode (to execute the programs registered within the NC unit) MEMORY Press the memory mode key Select a program to be executed. (This operation is referred to as “work number search.”) - Carry out the following procedure. Call either one of the following displays: POSITION display TRACE display...
- Page 453 Return to Library operation can be performed with no mouvement of the Z-axis. TUNING SV PARAM: If this item is selected, the NC unit automatically estimates the characteristics of the machine and the motor after automatic operation, then optimizes these characteristics according to actual machining conditions so that tool path errors do not occur, and sets the optimum characteristic data in the required parameter automatically.
- Page 454 Return to Library - Adjust the peripheral speed (number of revolutions) of the spindle using the spindle speed override keys. Spindle speed override keys D735S0015 - During automatic operation, the cutting conditions can be adjusted using the override keys. - See Chapter 3, “CHANGING THE CUTTING CONDITIONS”, for a detailed description of the usage of the override keys.
- Page 455 Return to Library Press the CYCLE START button. Î The automatic operation will start. - The CYCLE START button lamp stays on while automatic operation is in progress, and turns off when automatic operation terminates. Start button D735S0017 Note: Before pressing the CYCLE START button, make sure that the READY indicator lamp is Tape operation mode (to execute EIA/ISO programs stored on external media) Connect the external unit to the NC unit.
- Page 456 Return to Library 1-2-2 Restart operation Select the RESTART menu function if machining that has been aborted for some reason is to be restarted from the corresponding portion of the program. The procedure up to activation of the restart operation is described below. The following description assumes that operations, such as a search for the work number of the program you may wish to restart, selection of execution conditions, etc.
- Page 457 Return to Library Input restart command data. ‡ @ ‡ A ‡ B ‡ C D735S0018E Work No. • Unit No. • Sequence No. • If the unit specified in • is repeatedly used in the program, specify how many times of •...
- Page 458 Return to Library Input 2 by pressing 2 and , in that order. REPEAT NUMBER Restarting from the position in the subprogram by the third use is to take place. Input 3 by pressing , in that order. Here, if 1, for example, is input, automatic operation will restart from the drill sequence of the drill unit in the subprogram (WNo.
- Page 459 Return to Library Example 1: If program structure is as shown below: Main program (WNo. 10) UNo. SNo. SAME unit OFS-1 OFS-2 WPC unit DRILLING unit CTR-DR DRILL Subprogram (WNo. 11) FIG: PT UNo. SNo. SUB PRO unit SAME unit (WNo.
- Page 460 Return to Library To restart from machining order (4), input data as follows: SUB PROG. No. = 10 UNIT No. = 2 SEQUENCE No. = 2 REPEAT NUMBER = 2 Although restarting from the subprogram is not to take place, the offset operation must be regarded as analogous to the call of subprogram.
- Page 461 Return to Library The machining order is as follows. Work number and unit number Order number Tool of the program to be executed OFS-1 Spot drill WNo. 10, UNo. 2 OFS-1 Spot drill WNo. 10, UNo. 4 OFS-2 Spot drill WNo.
- Page 462 Return to Library Indicator lamps D735S0016 Press the RESTART menu key. Î The restart command data window will be displayed at the right side of the bottom of the screen. Input restart command data. ‡ @ ‡ A ‡ B ‡...
- Page 463 Return to Library Input “2” to restart from position b. Input “3” to restart from position c. Make sure that all the data items • to •above have been filled in and press the INPUT key. Î A search will be made for the restart position. - After the search is completed, the current status of S-, F-, T- and M-codes resulting from the restart position search will be indicated in the window.
- Page 464 Return to Library 1-1-3 MDI operation MDI operation refers to the operation in which data that corresponds to an EIA/ISO program is set by operator as required and executed. MDI operation is used to check particular machine operation, to carry out operational setup, to execute simple EIA/ISO program, etc. Basic operation Press the MDI key Î...
- Page 465 Return to Library Press the TOOL SELECT menu key. Î This will cause the display of TOOL SELECT to reverse and the message POCKET NUMBER? to be displayed. Using the appropriate numeric key(s), specify the identification number of the pocket that accommodates the tool to be moved to the tool change position.
- Page 466 Return to Library Press the CYCLE START button. Î This will cause the start button lamp to light up and the tool that was specified in procedural step (3) above to be mounted on the spindle. - When the tool has been mounted on the spindle, the start button lamp will go out. Setting the M-code Two methods are available for setting the M-code in the MDI data setting window.
- Page 467 Return to Library execution conditions and then press the start button. (For further details, see the description of procedural step (3) of Section 1-2-1, “Auto mode operation”). Measuring unit IN/OUT Except some models, the measuring unit must be moved out of its storage position before the tool length can be measured automatically or semi-automatically.
- Page 468 Return to Library Full-automatic tool-length measurement In the MDI operation mode, the length of a tool in the tool magazine can be measured automatically. The measured data will be automatically set in the TOOL LENGTH item of the TOOL DATA display. However, the tools whose lengths can be measured using this method are limited to tools whose tips are on the centerline of the spindle, that is, spot drills, drills, reamers, and taps.
- Page 469 Return to Library Press keys , and , in that order. Î This will cause “M196 T004 T005 T006 M197” to be displayed in the MDI data setting window. TOOL DATA display Display becomes reversed. D735S0022E Press the CYCLE START button. Î...
- Page 470 Return to Library The tool tip touches the top face of the plunger, forcing it downward. (See b.) The downward moving speed of the tool decreases and the tool tip pushes the plunger down to the measurement sensor action point. (See c.) When the skip signal turns on, the tool starts moving upward and returns to the machine zero-point.
- Page 471 Return to Library Tool length Machine zero-point Moving distance Plunger Measurement sensor action point (Skip signal turns on) Measuring unit Support Table column D735S0025 Fig. 1-2 Machine action in semi-automatic tool length measurement Move the measuring unit back into its storage position. Setting the pallet No.
- Page 472 Return to Library Setting the spindle-tool No. The identification number of the tool currently mounted on the spindle is to be registered by this operation. The identification number of the tool currently mounted on the spindle will still remain stored within the memory of the NC equipment even after power has been turned off. This operation should be carried out only when tools have been manually changed, when the tool has been manually dismounted from, or mounted onto the spindle.
- Page 473 Return to Library Group-number specification for tool management Tool change with group-number specification In a tool-management system which applies group numbers for T-code specification in EIA/ISO programming, the MDI tool-change operation using the TOOL CHANGE menu function can also be managed by specifying 8-digit group numbers.
- Page 474 Return to Library Parameters related to TOOL CHANGE and TOOL SELECT Pocket-number specification Group-number specification F94 bit 4 Group number (Tool searching) Tool (pocket) number If the EIA/ISO option is not provided, only pocket-number specification is valid, irrespective of the value of parameter L51.
- Page 475 Return to Library SELECTING EXECUTION CONDITIONS The following functions are available with the execution conditions selection menu or key for automatic operation: Optional Stop Dry Run Machine Lock Work Light Block Skip (for EIA/ISO programs only) Single Block Comparison Stop Z-axis Cancel MST Lock ATC Stop...
- Page 476 Return to Library Remark: Performing the operation step (1) again makes this function inactive. 2-1-2 Description If the above procedure is followed by automatic operation, it will stop when the execution of the block containing M01 is completed. Pressing the CYCLE START button causes automatic operation to be restarted from the next block.
- Page 477 Return to Library Adjust the feedrate using the cutting feed override keys. 2-2-2 Description - When the above procedure is followed by automatic operation, the program will be executed using the adjusted feedrate data. - Carrying out procedural step (1) above during automatic operation nullifies the programmed feedrate and the manual cutting feedrate will be selected.
- Page 478 Return to Library Remark: Performing the operation step (1) again makes this function inactive. Block Skip Block Skip refers to the function with which the specific blocks can be optionally skipped during program execution. This function is only valid for EIA/ISO programs. 2-5-1 Procedure Include a slash in the starting part of the block(s) to be optionally skipped.
- Page 479 Return to Library Comparison Stop Comparison Stop refers to the function with which the automatic operation can be placed into the single-block stop in any position as occasionally specified with work No., sequence No. and block 2-7-1 Setting procedure Press the COMPARSN STOP menu key. è...
- Page 480 Return to Library - The machine operation has come to the comparison stop correctly as specified. - The system has entered the reset status (at the end of a cycle or by pressing the RESET key). Comparison stop is only available in MEMORY, TAPE , HARD DISK or IC memory card operation mode.
- Page 481 Return to Library The designation of such a block as mentioned above, however, can be validated for comparison stop by setting parameter F93 bit 6 to “1”. 13. Even if the succeeding block of M98 in the calling program is specified during comparison stop after the M99 block of the called program, the restarted operation will not come to a comparison stop at the required position.
- Page 482 When calculating the optimum data at any specific position of the machine When highly accurate machining is required To use this function, the Shape Correction Option and the MAZAK Precision Rapid Boring Tornado Option are required. Alarm 936: OPTION NOT FOUND (4, 0, 0) will occur if this function is...
- Page 483 Return to Library 2-11-1 Operation procedure Select an axis characteristics estimation program on the POSITION display. (See Note 2 below.) Move the spindle to a position near the actual machining location of the table using the manual pulse feed keys and the pulse handel. However, there is the need to move the Z-axis away from the workpiece so that they do not interfere.
- Page 484 Return to Library (2) For MAZATROL: Circular operation of 25 mm (0.98 in.) in radius and 10 mm (0.39 in.) in feed rate is repeated three times on the X-Y plane in the manual program mode unit. File Window Help D735S0051E 2-11-2 Function description After the above operations, when automatic operation is started, the characteristics estimation...
- Page 485 Return to Library Auto Tuning (AT_J_V1.11) Circular Error X axis center = –949970.5 (green: Ref. Value, red: F.B. value) Y axis center = –499979.5 Radius = 50000 Drawing scale = X 1000 1 µm/Div 98/11/24 JCF Identification Mesured Work Circular Circular Erase Data...
- Page 486 Return to Library - NOTE - 2-12...
- Page 487 Return to Library CHANGING THE CUTTING CONDITIONS During automatic operation, especially during test cutting, the cutting parameters specified in the program may require changing according to the shape of cutting chips, the status of its flyabout, the load status display of the spindle and axis driving motors on the POSITION display, the degree of as-finished surface roughness of the workpieces, and other factors.
- Page 488 Return to Library Cutting Feed Override Using the cutting feed override keys, the cutting feedrate specified in the program can be changed within the range from 0 to 200 percent. 3-2-1 Procedure Press the cutting feed override key - The cutting feedrate increases in 10% steps each time the key is pressed, and continuously increases when this key is pressed and held down.
- Page 489 Return to Library Spindle Speed Override Using the spindle speed override keys, the programmed rpm (revolutions per minute) value of the spindle can be changed within the range from 0 to 150 percent of the original value. 3-3-1 Procedure Press the spindle speed override key - The spindle speed increases in 10% steps each time the key is pressed, and continuously increases when this key is pressed and held down continuously decreses when...
- Page 490 Return to Library VFC Function VFC refers to the function that automatically overrides the cutting conditions in the actual program, such as feedrates, peripheral speeds (or number of revolutions), with the new data that have been set using the override keys. The VFC function can be used only for MAZATROL programs.
- Page 491 Return to Library By this time, the actual cutting feedrate and peripheral speed will have already been changed, but not yet the corresponding values in the program. Program Cutting feedrate: 30 mm/min Peripheral speed: 2.4 m/min Lamp turns off. D735S0036 Fig.
- Page 492 Return to Library AFC Function (Option) The AFC (Adaptive Feedrate Control) is a function that provides automatic control of the feedrate to prevent overloading of the spindle motor and the Z-axis servo motor. After detecting the cutting current load on the spindle motor or Z-axis servo motor, this function compares the current load value with the corresponding presetting (relative value in percentage terms with respect to the rated load) on the TOOL DATA display and then automatically changes the feedrate if any deviation from the preset value is found.
- Page 493 Return to Library 3-5-1 Setting the desired current load value Set the desired current load value in percentage terms on the TOOL DATA display. If the current load on the spindle motor is to be supervised, set the desired horsepower value (HP) (this renders the AFC function valid for the spindle).
- Page 494 Return to Library 3-5-2 Tools available with AFC and AFC supervisory modes The tools for which AFC can be executed and the modes of AFC supervision are listed below. Tool name AFC supervisory mode DRILL (Drill) E-MILL (End-mill) Spindle and Z-axis AFC OTHER (Special cutter) (Simultaneous) F-MILL (Face-mill)
- Page 495 Return to Library Z-axis AFC function Start of cutting End of cutting Rapid feedrate Idle Cutting cutting 100% AFC valid Feedrate Workpiece D735S0040 Fig. 3-5 Z-axis AFC function Note: When the Z-axis AFC function starts operating, the corresponding lamp in the machine status indicator window lights up.
- Page 496 Return to Library - NOTE - 3-10...
- Page 497 Return to Library STOPPING AUTOMATIC OPERATION All machine actions must be emergently stopped if any abnormalities occur during automatic operation, such as in the case where the tool is likely to contact the workpiece, the jig, etc. When machining has been executed to a certain extent, it may be also necessary to bring automatic operation to a halt so that you can check the finished status of the workpieces.
- Page 498 Return to Library Press the RESET key Î The alarm message EMERGENCY STOP will disappear. - The READY (ready for operation) indicator lamp will turn on to indicate that the emergency stop status has been released. Note: This procedure can be different according to the machine model. Reset Press the RESET key Î...
- Page 499 Return to Library Stopping by Changeover to a Manual Operation Mode Press one of the manual operation mode selector keys. Î The machine actions (movements of the spindle, axes, etc.) will stop immediately. Remark: Changing back to the original automatic operation mode and then pressing the CYCLE START button will let automatic operation restart.
- Page 500 Return to Library 4-5-2 Single-block stop using the SINGLE BLOCK key SINGLE BLOCK Press the key. Î The key lamp turns on to indicate that the Single Block function has become active and the machine actions will stop at the end of the block being executed. Program Stop Set previously M00 (M-code for program stop) in the program to be executed.
- Page 501 Return to Library MANUAL INTERRUPTION Interrupting automatic operation for you to carry out manual operations is referred to as manual interruption. Carry out manual interruption in cases that the tool path specified in the programs is to be shifted, that a damaged tool-tip is to be replaced, etc. To carry out manual interruption, first interrupt automatic operation using one of the following three methods: - Feed hold...
- Page 502 Return to Library TPS Function TPS refers to the function that lets the NC unit store the tool-tip position during manual interruption into the memory of the unit. With this function, those positions of the tool-tip at up to four different points during manual- interruption axis movement can be stored into the memory of the NC unit.
- Page 503 Return to Library 5-2-2 Storing the data of both the stop point of automatic operation and the passage point(s) existing during manual interruption Abort automatic operation. Change the automatic-operation mode over to any manual mode. - See the description of procedural step (2) in Section 5-2-1 above. Press the TPS menu key.
- Page 504 Return to Library 5-2-3 Storing the data of only the passage point(s) existing during manual interruption Carry out the same operation except the procedural step (3), as described in Section 5-2-2 above. Example: If, as shown below, the tool has been moved in order of a•b•c•d•e•N and the TPS menu key has been pressed at the points c and d: R: Rapid feed Stop point of...
- Page 505 Return to Library OPERATIONS POSSIBLE DURING AUTOMATIC OPERATION Data Rewriting 6-1-1 Data writing conditions Data setting and other operations on each display are restricted by the operational status of the machine at a particular time. Also, while program override lock/enable switch remains set to LOCK (writing disabled), writing or updating the current program or several other types of data cannot be performed.
- Page 506 Return to Library •: Possible ×: Impossible •: Impossible only for the program being executed. •: When parameter L57 is 0: Impossible 1: Possible PROGRAM LOCK/ENABLE switch status ENABLE LOCK Display Data item Operation Remarks Autom. mode Autom. mode Manu. Manu.
- Page 507 Return to Library...
- Page 508 Return to Library Notes:...
- Page 509 Return to Library TABLE OF CONTENTS (APPENDIX) Page STANDARD SPECIFICATIONS OF THE MACHINE......1-1 Major Machine Specifications ................1-1 Stroke Diagram and Spindle Interference Diagrams .......... 1-3 Spindle Speed-Power-Torque Diagrams............1-4 Table Dimensions ....................1-5 Sub table Dimensions ..................1-5 Workpiece Interference Diagram................ 1-6 ALARM LIST ...................2-1 M CODE LIST ..................3-1...
- Page 510 Return to Library - MEMO -...
Page 511: Major Machine Specifications
- Page 512 Return to Library Item Unit B-type ATC, Tool storage capacity Standard tool specifications magazine Option Tool selection system Random selection by magazine pocket number Automatic shorter path selection Tool shank type MAS BT-40 Max. tool diameter with adjacent mm (in) φ...
Page 513: Stroke Diagram And Spindle Interference Diagrams
Page 514: spindle speed-power-torque diagrams, page 515: sub table dimensions, page 516: workpiece interference diagram, page 517: alarm list.
- Page 518 Return to Library Alarm No. Sensor Detecting Alarm Name Description Machine Status (SQ Coil No.) the Alarm ILLEGAL TOOL FOR 1. Tool measuring cycle is executed for a Tool length measurement (F24) TOOL LGTH MEAS touch sensor or chip removing tool. cycle does not start.
- Page 519 Return to Library Alarm No. Sensor Detecting Alarm Name Description Machine Status (SQ Coil No.) the Alarm MAGAZINE DOOR The magazine door is open. Only display of message SQ31 (F37) OPENED AUTO TOOL CHANGE The [ATC STOP] menu key has been Stop just before the ATC (F38) STOP...
- Page 520 Return to Library Alarm No. Sensor Detecting Alarm Name Description Machine Status (SQ Coil No.) the Alarm ATC COVER SONSOR The ATC cover close sensor is not turned Spindle stop SQ23 (F59) (CLOSE) MALF. on although the ATC cover close command is executed, or the ATC cover close sensor is not turned off although the ATC cover open command is executed.
- Page 521 Return to Library Alarm No. Sensor Detecting Alarm Name Description Machine Status (SQ Coil No.) the Alarm NOT UNCLAMPED The TOOL UNCLAMP button is pressed Tool unclamp is disabled. Y300 (F83) (NOT STOP SPINDLE) while the [SPDL JOG] menu key is held pressed or while the spindle rotating.
- Page 522 Return to Library Alarm No. Sensor Detecting Alarm Name Description Machine Status (SQ Coil No.) the Alarm SET UP SWITCH WAS The automatic mode is selected when the (F116) SELECTED SET UP switch is ON. X10A CAN'T PLUS MOTION After the power supply is turned on, the axis Attempted operation is (F117) movement in the positive direction is...
- Page 523 Return to Library Alarm No. Sensor Detecting Alarm Name Description Machine Status (SQ Coil No.) the Alarm WARMING UP !! Indication of the machine status during Indication of the machine (F178) warm-up (not an error). status OPERATING Any of the following operation switches have Emergency stop (F181) SW.CONDITION...
- Page 524 Return to Library - MEMO -...
Page 525: Code List
- Page 526 Return to Library M Code Function ATC cover open Opens the ATC cover. Spindle oriented stop Stops the spindle in the oriented stop position (tool change angular position). Error detect ON Select the exact stop mode. Note: For details of the exact stop mode, refer to the instruction manual for the NC. Error detect OFF Cancels the M23 mode.
- Page 527 Return to Library M Code Function Tap coolant ON (option) Discharges tap coolant if the tap coolant unit is installed. Note: To top the tap coolant, execute M09. Tool life check Causes single block stop if tool life over alarm occurs with the tool mounted in the spindle. Note: To continue the operation, press the (CLEAR) key and the...
- Page 528 Return to Library M Code Function M195 Tool breakage detection ON (option) Executes a tool breakage detection cycle. This command is automatically specified right before the ATC cycle when M35 is entered in a MAZATROL program. Usually, this command is not used by the customer. M196 Tool length measurement mode ON (option) Turns on the tool length measurement mode.
- Page 529 Return to Library Note 1: Simultaneous processing impossible M codes Mazatrol permits the entry of up to four M codes in a single block. However, if M codes which cannot be processed simultaneously are entered in the same block, the following message is displayed and operation is suspended.
- Page 530 Return to Library - MEMO -...
This manual is also suitable for:
Rename the bookmark, delete bookmark, delete from my manuals, upload manual.
- Site Search
- ENGINEERING.com
- Eng-Tips Forums
- Tek-Tips Forums

Join Eng-Tips ® Today!
Join your peers on the Internet's largest technical engineering professional community. It's easy to join and it's free.
Here's Why Members Love Eng-Tips Forums:
- Notification Of Responses To Questions
- Favorite Forums One Click Access
- Keyword Search Of All Posts, And More...
Register now while it's still free!
Already a member? Close this window and log in.
Join Us Close
Industry’s Best-Selling Horizontals Machining Centers are in Stock Now
Put the rigidity, accuracy and value of Mazak's HCN Series to work in your shop today. Order your new automation ready #40 or #50 taper machine today for fast delivery.
What are you waiting for?
Due to severe storms in the area, Mazak Corporation is experiencing power, phone and email outages. We apologize for this inconvenience. Should you require service during this outage, please contact us at [email protected] .
We will notify you via our website and social media when normal service has been restored.
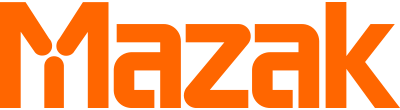
Leaders in the manufacture of advanced technology solutions including Multi-Tasking, HYBRID Multi-Tasking, 5-axis, milling, turning, CNC controls and automation.
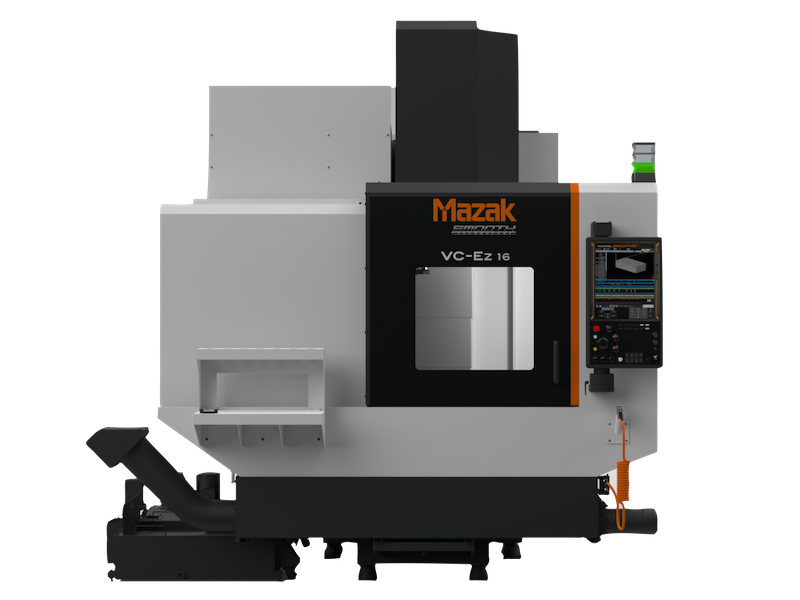
MACHINE DESCRIPTION:
The Kentucky-built VC-Ez 16 Vertical Machining Center combines a rugged spindle and a space-saving design with unprecedented affordability to put Mazak quality and reliability in virtually any shop. With a full range of spindle, auto tool changer and chip/coolant management options, the highly configurable machine meets many production needs. Enhanced operator ergonomics and a generous work area ease the loading and unloading of workpieces and tools, while an extremely fast traverse rate of 1,417 ipm in the X, Y and Z axes enables higher throughput.
The MAZATROL SmoothEz CNC includes full MAZATROL conversational programming and EIA/ISO programming compatibility, along with QUICK MAZATROL for easy part-program creation and confirmation and MAZATROL TWINS for offline part programming. SMOOTH Machining Configurator (SMC) provides real-time process optimization of cutting parameters and ITS (Intelligent Thermal Shield) manages thermal stability for greater reliability and improved part quality.
MACHINE CHARACTERISTICS:
- Rugged 25 hp, 12,000 rpm (standard) or versatile 29.5 hp, 15,000 rpm (optional) spindle
- Highly efficient 30-tool auto tool changer (50-tool option).
- Hybrid MX Roller Guide System improves rigidity, accuracy and reliability.
- Pre-tensioned ball screw system with support at each end.
- New space-saving machine design with optional chip management solutions.
Download VC-Ez Series Brochure
Download VC-Ez Flier
Get More Info

Machine Specifications
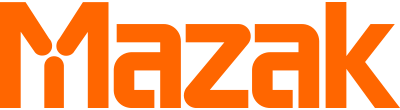
MACHINE DESCRIPTION:
The INTEGREX i-630 V Multi-Tasking machine brings together extreme versatility, speed, accuracy and ease of operation for manufacturers of medium and large sized complex components. The machine is a fusion of CNC turning center and machining center for full 5-axis machining and Done-In-One processing with powerful turning capability. This machine configuration works to eliminate multiple setups, fixtures, tools, handling and non-cut time.
MACHINE CHARACTERISTICS:
- 10,000-rpm 50-hp (5,000-rpm high-torque and 15,000-rpm high-speed optional) milling spindle with B-axis
- 550-rpm 50-hp turning speed
- Large square or round tables with full C-axis rotation for turning
- CAT 50 taper spindle
- Two-pallet changer
- Tool storage capacities from 43 to 348 tools
- Easy integration for PALLETECH system for automated manufacturing
Machine Specifications
- History of cooperation
- Areas of cooperation
- Procurement policy
- Useful links
- Becoming a supplier
- Procurement
- Rosatom newsletter
© 2008–2024Valtiollinen Rosatom-ydinvoimakonserni

- Rosatom Global presence
- Rosatom in region
- For suppliers
- Preventing corruption
- Press centre
Rosatom Starts Life Tests of Third-Generation VVER-440 Nuclear Fuel
- 16 June, 2020 / 13:00
This site uses cookies. By continuing your navigation, you accept the use of cookies. For more information, or to manage or to change the cookies parameters on your computer, read our Cookies Policy. Learn more

Mazak Alarms/Errors
Mazak plc alarm list.
Mazak plc alarm list for cnc machinists. Alarm List for the Mazak INTEGREX 300/400-II
For other Mazak alarm lists visit following pages.
- Mazak System/Drive error ( No. 1 – No. 99, No. 1000 – No. 1099 )
- Mazak CNC machine control error ( No. 100 – No. 199, No. 1100 – No. 1199 )
- Mazak PLC machine control error ( No. 200 – No. 399, No. 1200 – No. 1399 )
- Mazak CNC screen operation error ( No. 400 – No. 499, No. 1400 – No. 1499 )
- Mazak I/O error ( No. 500 – No. 599, No. 1500 – No. 1599 )
- Mazak MAZATROL program error ( No. 600 – No. 699, No. 1600 – No. 1699 )
- Mazak MAZATROL program error ( No. 700 – No. 799, No. 1700 – No. 1799 )
- Mazak EIA/ISO program error ( No. 800 – No. 899, No. 1800 – No. 1899 )
- Mazak EIA/ISO program error ( No. 900 – No. 999, No. 1900 – No. 1999 )
- Mazak Interference error ( No. 2100 – No. 2199 )
- 200 THERMAL TRIP (EMERGENCY STOP)
- 201 BREAKER TRIP
- 202 HYDRAULIC PRESSURE DOWN
- 203 AIR PRESSURE DOWN
- 204 SPINDLE CONTROLLER MALFUNCTION
- 205 MILLING CONTROLLER MALFUNCTION
- 206 OPEN FRONT DOOR (EMERGENCY STOP)
- 211 NOT OPERATED MCODE SIMULTA.
- 212 CHUCK OPEN/CLOSE SWITCH MALF.
- 213 ILLEGAL DESIGNATED TOOL No.
- 215 CHUCK SYSTEM MALFUNCTION
- 218 CHUCKING TYPE NOT SELECTED
- 220 TURRET POSITION SENSOR MALF.
- 221 TURRET CLAMP SENSOR MALFUNCTION
- 224 CHUCK SENSOR MALFUNCTION
- 225 FRONT DOOR SENSOR MALFUNCTION
- 231 TOOL EYE POSITION SENSOR MALF.
- 234 TOOL CLAMP SENSOR MALFUNCTION
- 236 PARTS-CATCHER SENSOR MALF.
- 243 MEASURING CONTROLLER MALF.
- 245 BAR-FEEDER CONTROLLER MALF.
- 248 EXTERNAL CONTROLLER (No.1) MALF.
- 250 SPINDLE START MISOPERATION
- 251 MILLING MOTOR ROTATION PROHIB.
- 252 AXIS MOVE MISOPERATION
- 253 OVERLOAD DETECTION
- 256 TURRET ROTATION PROHIBITED
- 257 ILLEGAL M-CODE
- 258 TNo. MISMATCH
- 259 MODE CHANGE IMPOSSIBLE
- 260 SLIDEWAY LUBRICATION ALARM
- 261 HEAD LUBRICATION ALARM
- 264 THERMAL TRIP X5 (SINGLE BLOCK)
- 267 BALL SCREW X44C LUBRICATION ALARM
- 270 SPINDLE ORIENT EXCEED TIME
- 272 TURRET INDEX EXCEED TIME
- 275 ROBOT SERVICE EXCEED TIME
- 276 ATC CYCLE EXCEED TIME
- 279 PARTS CATCHER CYCLE EXCEED TIME
- 282 CHUCK CLAMP EXCEED TIME
- 286 FRONT DOOR EXCEED TIME
- 292 SENSOR MALFUNCTION No. 3
- 293 SENSOR MALFUNCTION No. 4
- 297 CHUCK PRESSURE DOWN
- 300 START COND. ERR. (DOOR OPEN)
- 301 START COND. ERR. (TUR UNCLAMP)
- 302 START COND. ERR. (EXT RESET)
- 303 START COND. ERR. (EXT FEED HOLD)
- 308 C/S ERROR (TOOL EYE EXTEND)
- 310 C/S ERROR (TNo.MISMATCH)
- 311 C/S ERROR (TAIL STOCK QUILL)
- 312 C/S ERROR (PTCATCHER EXTEND)
- 313 C/S ERROR (C/S QUILL COMMAND)
- 320 TOOL UNCLAMP IMP. (M-SP ROT.)
- 321 MODE CHANGE IMPOSSIBLE (DURING ATC CYCLE)
- 322 RAPID MODE IMP. (ORIGIN RET UNF)
- 324 DIFF. MODE (ORIGIN RET UNFIN.)
- 325 TL. EYE EXT. IMP.
- 326 T/S QUILL EXT. IMP.
- 327 NOT IN ATC START POSITION
- 329 CHUCKING SELECTION PROHIBITED
- 340 CONDITION No.1 MISSING
- 341 CONDITION No.2 MISSING
- 361 TAIL ALARM
- 365 CARRIER CONTROLER MALFUNCTION
- 366 SHIFTER CONTROLER MALFUNCTION
- 374 OPERATING SWITCH FAULT
- 375 MOTOR & SERVO TURNING OFF ERR.
- 376 MAIN POWER TURNING OFF MALFUNCTION
- 377 COOLANT LEVEL LOW
- 378 HIGH PRESSURE PUMP THERMAL TRIP
- 379 TANK PRESSURE LOW
- 381 CONDITION MISSING (SET UP SWITCH)
- 382 COOLANT SYSTEM MALF.
- 383 ATC ALM: CARRIER&SHIFT. POS. MALF.
- 385 START COND. ERR. (Z-AXIS POS.)
- 386 ATC STOP
- 390 TOOL ON INTERFER ALARM
- 391 LD/ULD/ACHG CONDITION ALARM
- 392 MAGAZINE MANUAL INTERR.
- 394 ATC CONTROLLER MALF.
- 395 CHECK SENSOR MALF. (SEE D199)
- 397 MAGAZINE DOOR INTERLOCK
- 398 MAGAZINE COVER OPEN
- 399 MAINTE./ADJUST PARAM. ON

Mazak M Code List – INTEGREX
Mazak INTEGREX M code list for cnc machinists. Miscellaneous Function (M-Code) for the Mazak INTEGREX 300/400-III/III T/IIIS/IIIST Mazak M Code List M-codes Description M00 Program stop M01 Optional stop M02…

Mazak G Code List (M Series)
Mazak G code list for cnc machinists who work on MAZAK machining centers. Mazak G Code List G Code Function G00 Positioning G01 Linear interpolation G01.1 Threading with C-axis interpolation…

Doosan MX Series Alarm List
Alarm list for Doosan MX Series cnc machining centers/cnc lathe. ContentsDoosan MX Series CNCDoosan MX Series Alarm List Doosan MX Series CNC Alarms work for the following cnc machines, Doosan…

Mazak System / Drive Alarms Error Codes
Mazak System / Drive Alarms Error Codes List for MAZATROL MATRIX etc. For other Mazak alarm lists visit following pages. Mazak System/Drive error ( No. 1 – No. 99, No….

Mazak CNC Machine Control Alarms Error Codes
Mazak CNC machine control error List for MAZATROL MATRIX etc. For other Mazak alarm lists visit following pages. Mazak System/Drive error ( No. 1 – No. 99, No. 1000 – No….

Fadal PLC Alarms List / PLC Messages – FANUC 0i MC
Fadal PLC Alarms List / PLC Messages for Fadal Machining Centers (GE FANUC 0i MC CNC Controls). ContentsPLC AlarmsPLC Messages PLC Alarms ALARM DESCRIPTION 1002 DUAL DOOR SWITCH FAILURE 1003…

Doosan TT Series M-Code List
Doosan TT series M-code list for cnc machinists/programmers. M-Codes for both Upper unit and lower unit are given. ContentsDoosan TT Series CNCDoosan TT Series M-Code List Doosan TT Series CNC This list…
Fanuc M-Code List
M-code are cnc program instructions which help cnc machinist/programmer to control cnc machine hardware like chuck, tailstock, quill, coolant. Here are listed M-code which are mostly used on cnc lathe/mill…

Hust CNC Lathe Controller G Code List H4CL-T & H6C-T
Complete G-Code list for Hust Lathe CNC Controllers. A good reference for CNC machinists who work on CNC Lathe with Hust CNC controls. Following G code list works on following…

GSK CNC Alarm list – GSK980TD / GSK980TDb / GSK980TDc
GSK 980 TD / GSK 980 TDb / GSK 980 TDc alarm list for cnc machinists programmers who work on cnc lathe machines with GSK 980td / 980tdb / 980tdc…

Mazak G Codes (T Series)
Mazak G code list for cnc machinists who work on Mazak INTEGREX 300/400-III/III T/IIIS/IIIST cnc machines. Mazak G Codes G Code Function G00 Positioning G01 Linear interpolation G01.1 Threading with…

Haas Parameter List
Haas parameter list (mill/lathe) for cnc machinists who work on Haas cnc lathe/mill. Parameters are seldom-modified values that change the operation of the machine. These include servo motor types, gear ratios,…

Hurco Lathe M Codes
Complete list of Hurco lathe M Codes. CNC Machine M-Codes are used to control machine functions like spindle rotation, coolant on off etc. Hurco Lathe M Codes M00 – Program Stop…

Mach3 Mill G Code List
ContentsMach3 CNCMach3 G Code List Mill Mach3 CNC Mach3 is a software package which runs on a PC and turns it into a very powerful and economical Machine Controller. Mach3…

Hust H6C-T Lathe CNC Controller M-Codes
Complete M-Code list for CNC machinists who work on CNC Lathe machines with Hust H6C-T CNC Controller. ContentsFor Hust CNC G-CodesM-Codes for Hust H6C-T Lathe CNC Controller For Hust CNC…

G71 Longitudinal Roughing Cycle Mazak CNC Basic Programming Example
CNC basic programming exmaple for cnc programmers/machinists who work on Mazak / Fanuc cnc controls. This cnc code example shows the use of G71 Longitudinal Roughing Cycle. ContentsG71 Turning CycleProgramming…

Mazak CNC Screen Operation Alarms Error Codes
Mazak CNC screen operation error list for MAZATROL MATRIX etc. For other Mazak alarm lists visit following pages. Mazak System/Drive error ( No. 1 – No. 99, No. 1000 – No….

Tormach G code List
Complete Tormach G code reference. CNC machinists can download Tormach PCNC 1100 and Tormach PCNC 770 manuals Tormach Manuals Download. Tormach G code List G00 – Rapid positioning G01 – Linear…

Mazak G01.1 Threading with C-axis interpolation Example
/*MAZATROL MATRIX For INTEGREX IV Programming EIA/ISO Mazak G01.1 command in the milling mode enables a simultaneous interpolation on the C-axis and the X- and/or the Z-axis for straight, tapered…

Mach3 Turn G-Code List
Mach software has evolved to be the best available PC CNC software on the market. Not only is it extremely affordable to industry, and the hobbyist, it is pioneering in…
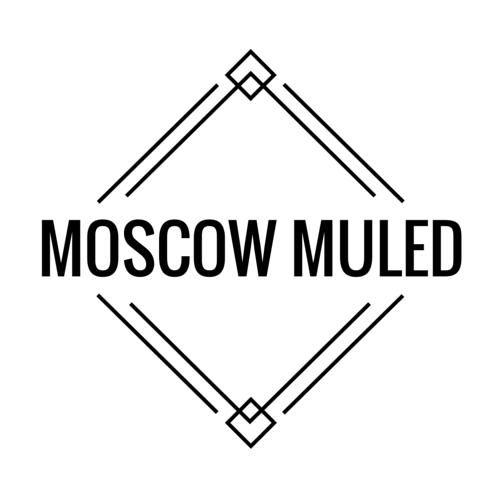
Moscow Muled
Why do moscow mules come in copper mugs.
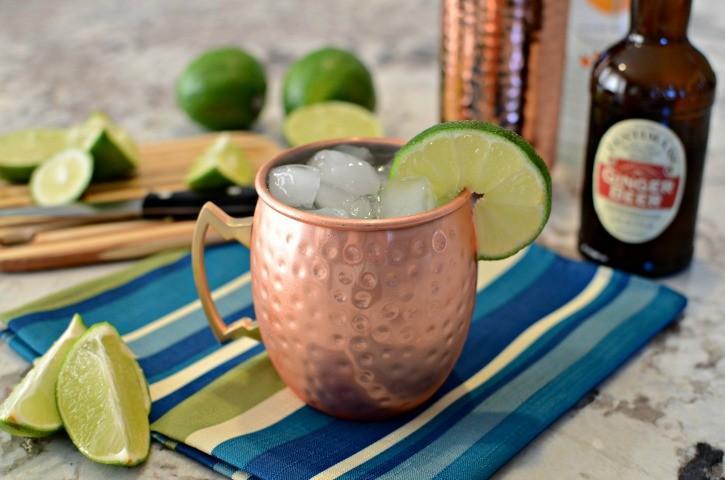
Oct 18, 2019
Have you ever wondered why the Moscow Mule cocktail is served in a copper mug? In this post, we answer that question in detail. As it turns out, the answer is partly based on historical events and partly based on the extra "kick" that copper brings to this classic cocktail. Let's dive in!
Introduction

A remarkable cocktail is something you notice from across the room, easily identified by the signature drinking vessel it's served in. Few are more distinct than the burnished copper mug of a Moscow Mule.
Great cocktails aren't just alcohol and mixers––they should be something more, a full sensory experience from beginning to end. It starts as you observe the precise convergence of ingredients in a golden ratio that blossoms into flavors and aromas of citrus and spicy ginger. It is then delivered into an ice-filled copper mug and garnished with fresh mint and a slice of lime. Finally, it is presented before you, shiny and cold, compelling you to taste.
The copper mule mug not only tells the story of the drink it contains, but also is essentially functional to the full experience. You might already know that the cone-shaped bowl of a long-stemmed Martini glass was designed so that olives would stand perfectly upright, and the elegantly curvaceous welled Margarita glass was designed to add ample salt, sugar and garnishes.
But why are Moscow Mules served in copper mugs?
Inquiring minds want to know, so this article will sum up the science and history of why traditional Moscow Mules come in copper mugs, and other legit benefits of serving cocktails in pure copper mugs. This includes:
A Brief History of the Moscow Mule
The science of using copper mugs.
- How Copper Mugs Amplify the Taste & Aroma of your Moscow Mule
- The Enhanced Experience of Drinking from a Pure Copper Mug
The origin of this timeless cocktail is the tale of the American Dream. One fateful day in 1941 , three struggling entrepreneurs had a serendipitous meeting at the Cock 'N Bull bar on the Sunset Strip in Hollywood: A bar owner passionate about his unpopular home-brewed ginger beer, a businessman who took a big chance and purchased Smirnoff vodka, and a Russian immigrant with a cache of copper mugs she couldn't seem to sell. That day, the unlikely trio wisely decided to join forces in a bold venture that would not only save their individual businesses, but also create an iconic American cocktail.
Essentially, the Moscow Mule is the most successful marketing campaign in cocktail history. At a time when most Americans had never even heard of vodka, this cocktail introduced them to the traditional Russian alcohol, and established Smirnoff as a necessity in both bars and homes alike.
Thanks to celebrity endorsement, the Moscow Mule soon took the Hollywood cocktail scene by storm, and quickly became the most beloved mixed drink of the 1950's.
It's popularity understandably waned during the Cold War, and it was briefly re-branded as the Smirnoff Mule to distance itself from communism. However, the recent cocktail renaissance of the 21st century has seen the Moscow Mule come kicking back, as evidenced by lists like Esquire's Top 10 Cocktails of 2019 , and Business Insider's 8th Best-selling Cocktail in the World, 2018 .
But the answer to why Moscow Mules are served in copper mugs goes much further than a conveniently clever alliance between co-founders desperate for a big break. The story of the Moscow Mule is both the struggle of the immigrant searching for success, and the flashy lifestyle of the rich and famous.
It boasts a simple recipe , yet a complex flavor profile, encapsulated in a shiny copper mug. And as delicious and refreshing as the Moscow Mule may be, it's the copper mug that makes the cocktail so extraordinary. Like the drink itself, the pure copper mule mug is a balance of form and functionality.

The most scientific benefit of the copper mug is its ability to regulate temperature. When a drink is served in a copper mug, it gets cold fast––and stays that way.
Copper is a renowned thermal conductor that will keep your beverage frosty in any weather, and is one of the reasons the traditional Moscow Mule has become synonymous with summer. Add a little ice, and the copper chills drinks instantly, and sustains a refreshingly icy rim with every sip.
Because copper is such an excellent conductor, it can keep your cold beverages colder for longer. The downfall of many ill-fated cocktails on a hot summer day is melting ice. Copper mugs stay brisk, and don't disrupt the recipe's ratio, so the simple yet distinct flavors of the Moscow Mule remain strong till the last drop.
Another important feature of the solid copper Moscow Mule mug is the handle. Much like the stem of a wine glass, the copper mug handle keeps the nearly 100 degree body temperature of your hand from impacting the status of your deliciously frosty cocktail.
How Copper Mugs Amplify the Taste and Aroma of Your Moscow Mule
If you want to know what a Moscow Mule tastes like, purists would insist the only way to experience it is in a 100% copper mug. Aside from being a great American tradition, copper mugs offer some unique enhancements to both the flavor and aroma of the Moscow Mule (or almost any finely-crafted cocktail).
Although subjective, most discerning drinkers would agree that copper mugs imbue cocktails with a superior taste. Experts explain that the copper oxidizes the vodka upon contact, thus enhancing the flavor profile and potency of the aromatics.
The intense cold of the copper also creates more stability in the bubbles of the ginger beer carbonation, and balances the tangy citrus of the lime with the earthy spice of the ginger.
For the skeptics out there, the theory of superior taste is easily verifiable. Simply make or order two Moscow Mules––one served in a plastic cup, and one served in a copper mug. Take a moment to inhale deeply, enjoy a big sip, and let your senses be the judge.
The epiphany should take a matter of moments, and you soon realize why a Moscow Mule is best served in a copper mug, and why any other cup or glass is vastly inferior. The difference can be so vivid, you might even consider drinking all your favorite beverages from copper mugs, even hot tea and coffee!
The Enhanced Experience of Drinking From a Pure Copper Mug
Throwing back shots with reckless disregard is a great way to get hammered, but a terrible way to enjoy something delicious. People order cocktails for the full package––observing its creation, revelling in its presentation, and slowly savoring its captivating story and unique taste.
Not only is a cocktail a well-balanced combination of spirits and mixers, it's also about the aesthetic and function of the vessel it's served in. A cocktail should be an object of inspired beauty, presented thoughtfully in a suitable glass or mug and garnished appropriately. It should take time, because it's made by hand.
Although the copper mug has become the symbol of Moscow Mules, it can also pair exquisitely with many other cocktails. Many people seem drawn to the shine and nostalgia of the metal, and Mixologists seem impressed by the scientific properties of the copper mug. Other drinks prominently featured in copper mugs include Dark 'n Stormy, Mescal, Gin & Tonic, and Cuba Libre.
No matter how frosted a beer glass gets, nothing can keep a mixed drink colder than a copper mug. The sensation when one's lips touch the ice-cold rim with every sip is part of the unique experience.
The flavors are heightened, the aromas amplified, and the balance of vodka, lime juice and ginger beer is never watered-down by melting ice. Provided your Moscow Mule is served in a pure copper mug, the last sip should be just as robust and enjoyable as the first.
The benefits of drinking from copper mugs aren't a newfound discovery. In fact, copper has been the preferred metal for drinking vessels for thousands of years.
Gurus in India have been using copper mugs for hundreds of years, and copper goblets called Escra have been found in ancient Irish ruins. Even American settles in 1645 drank exclusively from a massive tankard made of pure copper, known today as the Virginia Tankard .
The Moscow Mule is a classic drink served in a magnificent copper mug because it tells a compelling story, and enhances your consumption experience. It is an unforgettable drink because it's served in a mug that is both more beautiful than and functionally superior to glass.
Three Reasons Moscow Mules Come in Copper Mugs
The reason your Moscow Mule is served in a copper mug is not a fluke. It is not because it's the latest trendy hipster craze. It's not just a marketing ploy (although it definitely started out as one), nor is it a conspiracy by the lobbyists for Big Copper.
Moscow Mules come in copper mugs for three reasons: taste, temperature, and presentation.
The unique experience of drinking a Moscow Mule is a balanced combination of these three elements. It's also the reason this drink is not only the most recognizable, but also consistently one of the most popular drinks in global cocktail culture history.
Taste: The natural properties of the copper oxidize the alcohol, resulting in powerful aromatics and superior flavors. The bubbles of the ginger beer stay fizzy, and perfectly counter the acidity of the fresh lime juice. It's spicy yet refreshing. Simply put, it's delicious!
Temperature: Copper is an ideal thermal conductor, instantly chilling your beverage upon creation, and maintaining a consistently arctic temperature. This prevents the ice from quickly melting and dulling the cocktail ratio, while keeping the rim refreshingly frosty with every sip. The handle also keeps your hot little fingers from fluctuating the temperature with every touch.
Presentation: A glinting copper mug looks authentic and catches the eye. It is vintage, yet modern, and tells a story of creativity, charm and resilience. It is instantly recognizable, and makes for a fine looking beverage. Yes please!
The Bottom Line
The copper mug is iconic, a great American tradition of nearly 80 years, and is the only proper way to drink a Moscow Mule. Cheers!
Did You Enjoy This Article?
Thank you for reading! If you enjoyed this article, you might also like the following articles: How to Clean and Care for Copper Mugs: The Definitive Guide and Why You Should Only Use Moscow Mule Copper Mugs With Stainless Steel Lining
Relevant Products
Moscow Mule Copper Mug
Leave a comment
Subscribe to our newsletter.
Receive exclusive deals and our latest blog posts straight to your inbox!

COMMENTS
thermal trip is mazak speak for a tripped motor overload it means a motor is jamed or burned up the "thermal" part is refering to a thermal overload seeing a higher than normal current draw which is sensed by the temp in overload portion of the motor starter . G. ghandee Plastic. Joined Apr 9, 2014 Location Greece.
Page 72 If the cause is unknown, contact - (The same alarm occurs again soon your local Mazak Technical Center. even when the thermal relay is reset after cooling the motor.) 5-10-2 Resetting the thermal relay If alarm message "AL 217 THERMAL TRIP" "AL 014 CONVEYOR THERMAL TRIP" is displayed, any of the following thermal relays is ...
Double check around your m/c and look for any junction box's large enough to hold a contactor thats probably were you will find it not in the main cabinet. Rleu (Industrial) 16 Jun 04 18:21. Check the motor starter in the controll cabinet, If thats not it some of the motors have a thermal sensor built in which can not be reset without taking ...
Description Thermal relay for the hydraulic unit has tripped. Check and remedy Check that the hydraulic unit motor is normal, and then turn the power off and on. Mazak Alarm 200 THERMAL TRIP (EMERGENCY STOP)
Mazak Alarm 264 THERMAL TRIP X5 (SINGLE BLOCK) Mazak Alarm 264 THERMAL TRIP X5 (SINGLE BLOCK) Description. Thermal relay F13 for the coolant motor has tripped. Thermal relay F14 for the chip conveyor has tripped. Check and remedy. Check the regarding unit (e.g. chip conveyor for clogging with chips) and then reset the thermal relay.
Summary of Contents for Mazak VTC-200B. Page 1 This Manual is published to assist experienced personnel on the operation, maintenance and/or programming of Mazak machine tools. All Mazak machine tools are engineered with a number of safety devices to protect personnel and equipment from injury or damage. Operators should not, however, rely...
Description The thermal relays in the coolant unit of a machine of the high-pressure coolant specifications have become tripped. Check and remedy Check the thermal relays of the coolant unit. Mazak Alarm 378 HIGH PRESSURE PUMP THERMAL TRIP
thread281-305722. I am getting alarm 200 on a very old Mazak M5 Mazatrol T plus controller which states "THERMAL TRIP (EMERGENCY STOP)" and in the parameter list manual it says "A motor ON/OFF thermal relay switch has tripped". I have tried taking every motor on the machine out of the equation and have checked the transformer.
Measurement program can be easily produced. It automatically updates work coordinate and tool compensation using measurement results. After the measurement is performed, The measurement results can check using the report function. Smooth Set and Inspect is pre-installed on MAZATROL Smooth CNC, Customers can use the software operation for free.
MACHINE DESCRIPTION: The Kentucky-built VC-Ez 16 Vertical Machining Center combines a rugged spindle and a space-saving design with unprecedented affordability to put Mazak quality and reliability in virtually any shop. With a full range of spindle, auto tool changer and chip/coolant management options, the highly configurable machine meets ...
The INTEGREX i-630 V Multi-Tasking machine brings together extreme versatility, speed, accuracy and ease of operation for manufacturers of medium and large sized complex components. The machine is a fusion of CNC turning center and machining center for full 5-axis machining and Done-In-One processing with powerful turning capability. This ...
Mazak Alarm 264 THERMAL TRIP X5 (SINGLE BLOCK) Description Thermal relay F13 for the coolant motor has tripped. Thermal relay F14 for the chip conveyor has tripped. Check and remedy…
War Robots Gameplay and Vlog of Manni's Trip To Pixonic in Moscow - plus some fun WR Insights.🡒Join our Discord Community Server - the largest War Robots Se...
The aim of tests is to study mechanical stability of RK3+ components under thermal-hydraulic and dynamic conditions, which are close as possible to full-scale operation. Dukovany NPP with 2040 MWe of installed capacity has four power units powered by VVER-440 reactors which were commissioned one by one in 1985-1987. The plant generates about 13 ...
On the basis of measurements of electric and physical properties an analysis is made of the heat transfer mechanism of these compounds. It has been found that the thermal conductivity in Ag 2 Se is determined by a phononic and an electronic component and that of Ag 2 Te by a phononic, an electronic, and a photonic component.
Mazak PLC Alarm List. 200 THERMAL TRIP (EMERGENCY STOP) 201 BREAKER TRIP. 202 HYDRAULIC PRESSURE DOWN. 203 AIR PRESSURE DOWN. 204 SPINDLE CONTROLLER MALFUNCTION. 205 MILLING CONTROLLER MALFUNCTION. 206 OPEN FRONT DOOR (EMERGENCY STOP) 211 NOT OPERATED MCODE SIMULTA.
The reason your Moscow Mule is served in a copper mug is not a fluke. It is not because it's the latest trendy hipster craze. It's not just a marketing ploy (although it definitely started out as one), nor is it a conspiracy by the lobbyists for Big Copper. Moscow Mules come in copper mugs for three reasons: taste, temperature, and presentation.